Method for manufacturing mtj memory device
a memory device and manufacturing method technology, applied in the direction of galvano-magnetic material selection, magnetic field controlled resistors, electrical devices, etc., can solve the problems of reducing the efficiency of mtj devices, and forming pillar-like mtj devices without shunts, so as to reduce the re-deposition of material and reduce damage
- Summary
- Abstract
- Description
- Claims
- Application Information
AI Technical Summary
Benefits of technology
Problems solved by technology
Method used
Image
Examples
first embodiment
[0026]FIGS. 5A and 5B-5D illustrate two alternative embodiments for etching the MTJ layer stack to the barrier layer 315 of the MTJ structure. In particular, FIG. 5A illustrates the etching step. As shown, the etching step result in formation of MTJ pillar 330 having a width defined by the width of photoresist 319. As noted above, in the exemplary embodiment, the barrier layer 315 is formed from an oxide of magnesium (MgO). It should be appreciated that processing of MTJ layer stack into MTJ pillar shaped devices requires precise control of the etching depth through all of the stack layers. The barrier resistance control is partially determined based on precision of the etching on the free layer 316 and the barrier layer 315. To eliminate shunting and to reduce the free layer 316 edge damage, stopping at the barrier layer 315 across the wafer is necessary to eliminate the re-deposition on the barrier layer 315. Furthermore, it should be appreciated that stopping at the barrier layer...
second embodiment
[0028]FIGS. 5B-5D illustrate a second embodiment for etching the MTJ layer stack according to the exemplary embodiment. In particular, FIGS. 5B-5D illustrate etching using multiple ion beam etching and reactive ion etching techniques (both shown in FIG. 5B-5D as downward facing arrows for illustrative purposes). First, after photoresist 319 is applied as shown in FIG. 4, the hard mask 318 is etched using reactive ion etching and the upper layers 317, including perpendicular polarizer 250, down to TaN capping layer 238 (which is illustrated as part of upper layers 317) are etched using ion beam etching. These two etching steps are collectively shown in FIG. 5B.
[0029]It should be appreciated that similar manufacturing methods for MTJ pillars have not been developed for layer stacks having perpendicular polarizers 250 and the like. Therefore, conventional manufacturing methods do not contemplate a separate ion beam etching after the photoresist 319 has been etched using reactive ion et...
PUM
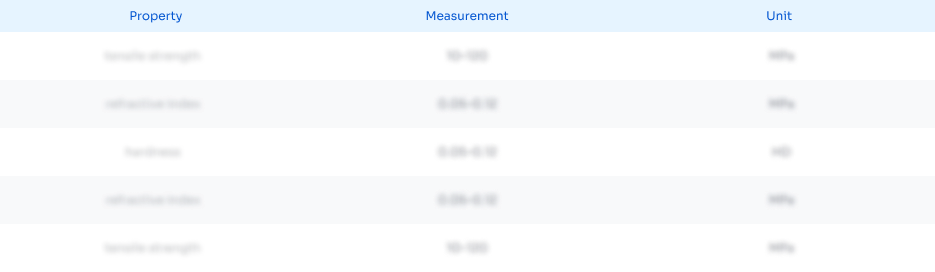
Abstract
Description
Claims
Application Information

- R&D
- Intellectual Property
- Life Sciences
- Materials
- Tech Scout
- Unparalleled Data Quality
- Higher Quality Content
- 60% Fewer Hallucinations
Browse by: Latest US Patents, China's latest patents, Technical Efficacy Thesaurus, Application Domain, Technology Topic, Popular Technical Reports.
© 2025 PatSnap. All rights reserved.Legal|Privacy policy|Modern Slavery Act Transparency Statement|Sitemap|About US| Contact US: help@patsnap.com