System, apparatus and method for abrasive jet fluid cutting
- Summary
- Abstract
- Description
- Claims
- Application Information
AI Technical Summary
Benefits of technology
Problems solved by technology
Method used
Image
Examples
Embodiment Construction
[0043]Reference will now be made in detail to the present embodiments of the disclosure, examples of which are illustrated in the accompanying drawings. Wherever possible, the same reference numbers will be used throughout the drawings to refer to the same or like parts (elements).
[0044]To help understand the advantages of this disclosure the accompanying drawings will be described with additional specificity and detail.
[0045]The present disclosure generally relates to methods and apparatus of abrasive-jet-fluid cutting through well bore casing or similar structure. The method generally is comprised of the steps of positioning a jetting-shoe and jet-nozzle adjacent to a pre-selected location of casing in the annulus, pumping a motive fluid containing abrasives through the jet-nozzle such that the fluid is jetted there from cutting through the casing, while moving the jetting-shoe and jet-nozzle in a predetermined programmed vertical axis and 360 degree horizontal rotary axis.
[0046]I...
PUM
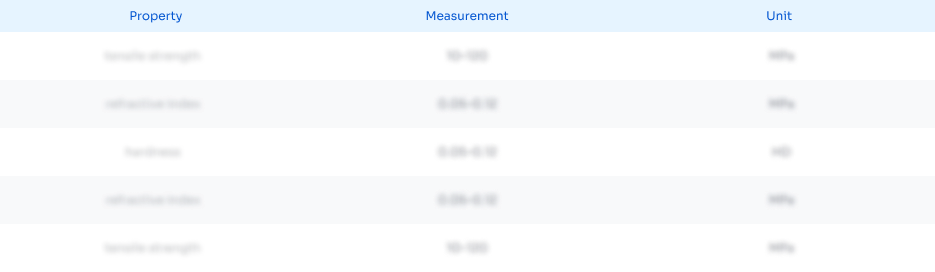
Abstract
Description
Claims
Application Information

- R&D
- Intellectual Property
- Life Sciences
- Materials
- Tech Scout
- Unparalleled Data Quality
- Higher Quality Content
- 60% Fewer Hallucinations
Browse by: Latest US Patents, China's latest patents, Technical Efficacy Thesaurus, Application Domain, Technology Topic, Popular Technical Reports.
© 2025 PatSnap. All rights reserved.Legal|Privacy policy|Modern Slavery Act Transparency Statement|Sitemap|About US| Contact US: help@patsnap.com