Process and appratus for producing gas hydrate
a technology of gas hydrate and process, applied in the direction of gaseous fuel, liquefaction, lighting and heating apparatus, etc., can solve the problems of small filling amount, small decomposition stability, rapid evaporation, etc., and achieve the effect of reducing the power of cooling liquid refrigerant, high specific heat, and high heat capacity
- Summary
- Abstract
- Description
- Claims
- Application Information
AI Technical Summary
Benefits of technology
Problems solved by technology
Method used
Image
Examples
Embodiment Construction
[0091]Hereinafter, an apparatus for producing a gas hydrate according to the present invention will be described with an illustration thereof.
[0092]As shown in FIG. 1, the apparatus for producing a gas hydrate according to the present invention includes: a generating device 1 for generating a gas hydrate h by subjecting a raw-material gas g1 and raw-material water w1 to a hydration reaction; a dewatering device 2 for discharging water from a gas hydrate slurry h1 containing the gas hydrate h generated by the generating device 1; and a molding device 3 for forming pellets h3 by compressing a gas hydrate h2 dewatered by the dewatering device 2.
[0093]The generating device 1 includes: a pressure-tight container 1A connected to a supply pipe L1 for the raw-material gas g1 and to a supply pipe L2 for the raw-material water w1; and a stirring blade 1B for stirring an aqueous solution in the container 1A. A bottom portion of the pressure-tight container 1A is provided with a sparger 10 for ...
PUM
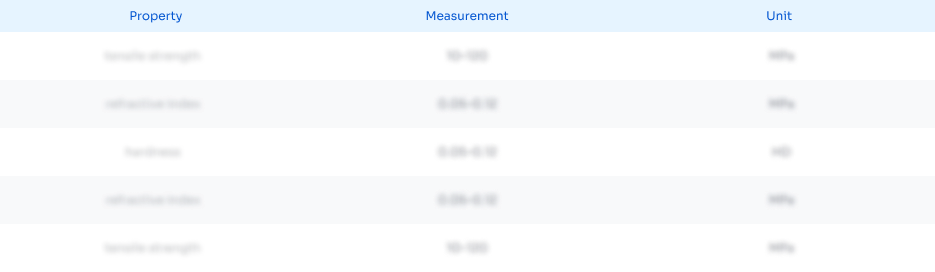
Abstract
Description
Claims
Application Information

- R&D Engineer
- R&D Manager
- IP Professional
- Industry Leading Data Capabilities
- Powerful AI technology
- Patent DNA Extraction
Browse by: Latest US Patents, China's latest patents, Technical Efficacy Thesaurus, Application Domain, Technology Topic, Popular Technical Reports.
© 2024 PatSnap. All rights reserved.Legal|Privacy policy|Modern Slavery Act Transparency Statement|Sitemap|About US| Contact US: help@patsnap.com