System and method for cooling rocket engines
a rocket engine and cooling system technology, applied in the field of rocket engine cooling system, can solve the problems of insufficient surface tension device for no currently developed diaphragm tank technology for liquid oxygen, and no current demonstration of nitrous oxide and liquid oxygen surface tension devi
- Summary
- Abstract
- Description
- Claims
- Application Information
AI Technical Summary
Problems solved by technology
Method used
Image
Examples
Embodiment Construction
[0018]Referring to FIGS. 1-6, a cooling system 20 constructed in accordance with the teachings of the present disclosure for a propulsion system 21 is shown. The propulsion system 21 includes a rocket engine 22 and one or more propellant tanks 24, which can be in fluid communication with the rocket engine 22 to supply a propellant to the rocket engine 22 for combustion. In FIGS. 1-6, a monopropellant propulsion system is shown with only one propellant tank 24. In FIG. 7, a bipropellant propulsion system is shown having two propellant tanks 24. Accordingly, the present disclosure is applicable to any rocket engine regardless of the number and configuration of propellant tanks and oxidizer tanks used. The propulsion system 21 may also include a first heat exchanger 26 that is thermally coupled to the rocket engine 22. The cooling system 20 includes a second heat exchanger 28 that is thermally coupled to the propellant tank 24, and a coolant tank 30 configured to hold a coolant. The fi...
PUM
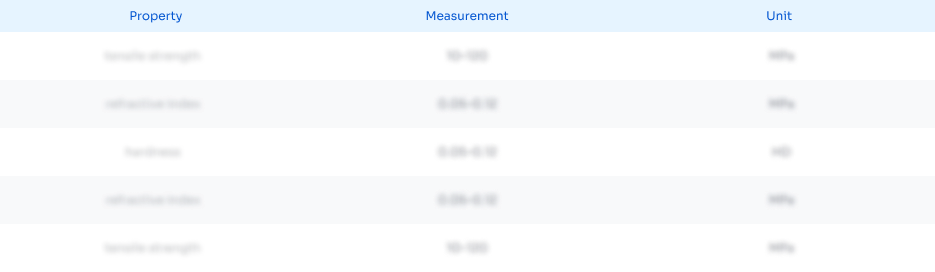
Abstract
Description
Claims
Application Information

- R&D Engineer
- R&D Manager
- IP Professional
- Industry Leading Data Capabilities
- Powerful AI technology
- Patent DNA Extraction
Browse by: Latest US Patents, China's latest patents, Technical Efficacy Thesaurus, Application Domain, Technology Topic, Popular Technical Reports.
© 2024 PatSnap. All rights reserved.Legal|Privacy policy|Modern Slavery Act Transparency Statement|Sitemap|About US| Contact US: help@patsnap.com