Method and Apparatus for High Temperature Heat Treatment of Combustible Material in Particular Waste
- Summary
- Abstract
- Description
- Claims
- Application Information
AI Technical Summary
Benefits of technology
Problems solved by technology
Method used
Image
Examples
Embodiment Construction
[0041]In FIG. 1, a first exemplary embodiment is diagrammatically shown of an apparatus 1, according to the present invention, for high temperature heat treatment of combustible material, in particular municipal solid waste (waste products), or combustible waste of a desired nature, provided that the combustible waste is a solid and not explosive waste. The apparatus comprises a pyrolysis chamber 41, where the material 85 to treat is heated in a reducing environment, up to a temperature suitable for making a first molecular break of the substances present in the material, and a combustion chamber 42 within which a full combustion is achieved of the combustible material by introducing a predetermined flow of oxygen 8. The full combustion of the combustible material is carried out only in combustion chamber 42 of the apparatus 1 and produces, in particular, gas at high temperature that is directed back to pyrolysis chamber 41 in order to remarkably raise the temperature of pyrolysis. ...
PUM
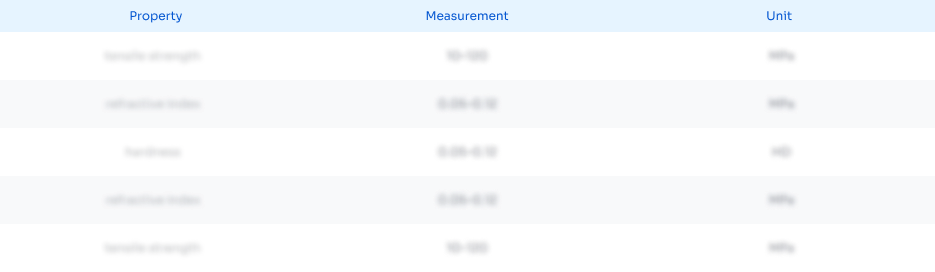
Abstract
Description
Claims
Application Information

- R&D
- Intellectual Property
- Life Sciences
- Materials
- Tech Scout
- Unparalleled Data Quality
- Higher Quality Content
- 60% Fewer Hallucinations
Browse by: Latest US Patents, China's latest patents, Technical Efficacy Thesaurus, Application Domain, Technology Topic, Popular Technical Reports.
© 2025 PatSnap. All rights reserved.Legal|Privacy policy|Modern Slavery Act Transparency Statement|Sitemap|About US| Contact US: help@patsnap.com