Methods and systems to facilitate operating within flame-holding margin
- Summary
- Abstract
- Description
- Claims
- Application Information
AI Technical Summary
Benefits of technology
Problems solved by technology
Method used
Image
Examples
Embodiment Construction
[0014]FIG. 1 is a cross-sectional view of an exemplary nozzle assembly 10. In the exemplary embodiment, nozzle assembly 10 is divided into four regions by function including an inlet flow conditioner (IFC) 12, a swirler assembly 14 with fuel injection, an annular fuel fluid mixing passage 16, and a central diffusion flame fuel nozzle assembly 18. Nozzle assembly 10 also includes a high pressure plenum 20 having an inlet end 22 and a discharge end 24. High pressure plenum 20 circumscribes nozzle assembly 10. Discharge end 24 does not circumscribe nozzle assembly 10, but rather discharge end 24 extends into a combustor reaction zone 26. IFC 12 includes an annular flow passage 28 that is defined by a solid cylindrical wall 30. Wall 30 defines an inside diameter 32 for passage 28, and a perforated cylindrical outer wall 34 defines an outside diameter 36. A perforated end cap 38 is coupled to an upstream end 40 of nozzle assembly 10. In the exemplary embodiment, flow passage 28 includes ...
PUM
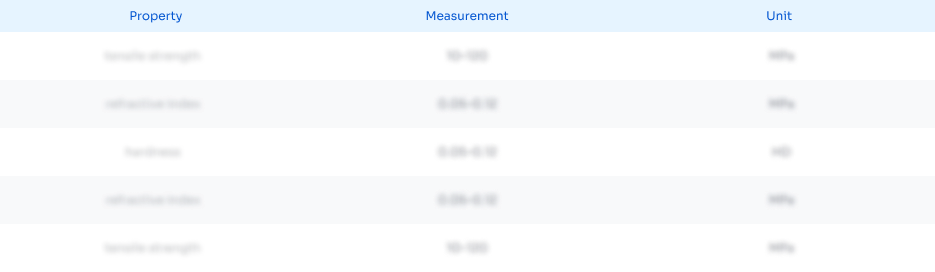
Abstract
Description
Claims
Application Information

- R&D
- Intellectual Property
- Life Sciences
- Materials
- Tech Scout
- Unparalleled Data Quality
- Higher Quality Content
- 60% Fewer Hallucinations
Browse by: Latest US Patents, China's latest patents, Technical Efficacy Thesaurus, Application Domain, Technology Topic, Popular Technical Reports.
© 2025 PatSnap. All rights reserved.Legal|Privacy policy|Modern Slavery Act Transparency Statement|Sitemap|About US| Contact US: help@patsnap.com