Method for Processing Substrate, Apparatus for Processing Substrate, Method for Conveying Substrate and Mechanism for Conveying Substrate
a technology for conveying substrates and substrates, applied in the direction of instruments, charge manipulation, furnaces, etc., can solve the problems of uneven distribution of gap spacers between two substrates in the bonded substrate, and achieve the reduction of suppressing warping inside the substrate, and reducing the time required for turning over a substrate
- Summary
- Abstract
- Description
- Claims
- Application Information
AI Technical Summary
Benefits of technology
Problems solved by technology
Method used
Image
Examples
first embodiment
[0084]In the following, the first embodiment of this invention is described in detail in reference to FIGS. 1 to 7.
[0085]FIG. 1 is a perspective diagram showing an apparatus for processing a substrate according to this invention as viewed from the left, and FIG. 2 is a perspective diagram showing the above described apparatus for processing a substrate as viewed from the right.
[0086]In FIGS. 1 and 2, an apparatus for processing a substrate 10 is mainly formed of a portion for mounting a substrate 1, where a fragile substrate is mounted, a portion for conveying a substrate 2, having a number of robots for conveying a substrate, a scribing portion 3, which scribes a substrate that has been conveyed by portion for conveying a substrate 2, and a breaking portion 4 for breaking a scribed substrate.
[0087]Examples of the configuration and the operation of apparatus for processing a substrate 10 are described in reference to FIGS. 1 and 2.
[0088]First, a cassette 11 for conveying a substrate...
second embodiment
[0120]In the following the apparatus for processing a substrate according to the second embodiment of this invention is described in reference to FIGS. 8 to 10.
[0121]Though, in the first embodiment, the distance between axis lines of the rotational axis of adjacent suction members is constant in robot for conveying a substrate 24 has suction members so that substrates which are placed on a table in advance at intervals which agree with the distance between the axis lines are sucked and turned over, in the second embodiment, an example of a robot for conveying a substrate having a configuration where the distance between the axis lines of the rotational axis of adjacent suction members is varied in accordance with the intervals of substrates which are mounted on a table in advance and then the substrates which are mounted on the table are sucked and turned over is described.
[0122]As shown in FIG. 8, a portion for turning over and sucking a substrate 70 has a frame 79 having a side pl...
third embodiment
[0134]In the following, the apparatus for processing a substrate according to the third embodiment of this invention is described in reference to FIGS. 11 to 14.
[0135]In the third embodiment, an apparatus for separating a substrate, which separates a substrate along a scribe line, is described as a modification which uses a robot for conveying a substrate 70 having a leaking mechanism 98 in pantograph form as described in the second embodiment.
[0136]That is to say, in the third embodiment, an example of a configuration which has a number of rotational axes to which suction members are attached, a portion for driving a rotational axis, which is the same as those used in the above described first and second embodiments, a frame to which the portion for driving a rotational axis and the number of rotational axes are attached so that the rotational axes can be rotated by the portion for driving a rotational axis, at least one suction member unit formed of a portion for shifting a rotati...
PUM
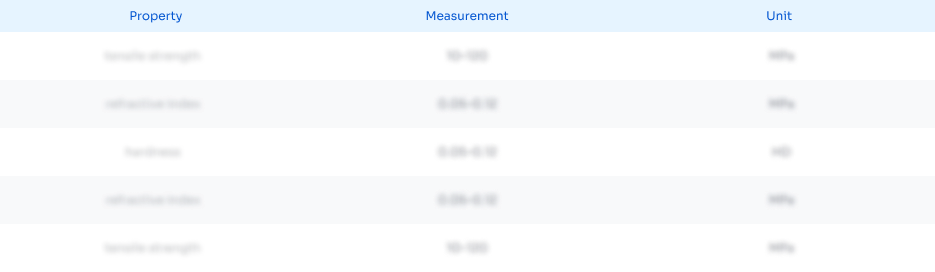
Abstract
Description
Claims
Application Information

- R&D
- Intellectual Property
- Life Sciences
- Materials
- Tech Scout
- Unparalleled Data Quality
- Higher Quality Content
- 60% Fewer Hallucinations
Browse by: Latest US Patents, China's latest patents, Technical Efficacy Thesaurus, Application Domain, Technology Topic, Popular Technical Reports.
© 2025 PatSnap. All rights reserved.Legal|Privacy policy|Modern Slavery Act Transparency Statement|Sitemap|About US| Contact US: help@patsnap.com