External heat engine of the rotary vane type and compressor/expander
- Summary
- Abstract
- Description
- Claims
- Application Information
AI Technical Summary
Benefits of technology
Problems solved by technology
Method used
Image
Examples
Embodiment Construction
[0020]In describing the preferred and alternate embodiments of the present invention, as illustrated in FIGS. 1-8, specific terminology is employed for the sake of clarity. The invention, however, is not intended to be limited to the specific terminology so selected, and it is to be understood that each specific element includes all technical equivalents that operate in a similar manner to accomplish similar functions.
[0021]Referring now to FIG. 1, illustrated therein is heat engine 100, having an outer housing 2 and a rotor 1 that rotates within the housing. Contained within the rotor 1 are a plurality of slots 12 and a plurality of sliding vanes 3 residing within the slots 12. The vanes 3 extend outwards to make contact with the inner walls of the housing 2.
[0022]Each vane 3 is connected to another vane 3 on the opposite side of the rotor 1 by one or more connecting linkages 13. The connecting linkages 13 that connect a pair of vanes 3 are horizontally offset from other connecting...
PUM
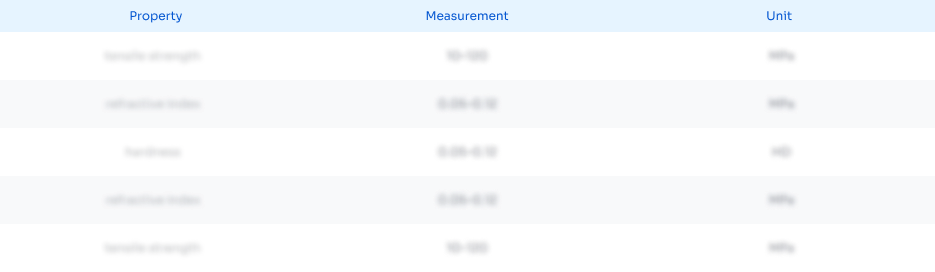
Abstract
Description
Claims
Application Information

- R&D
- Intellectual Property
- Life Sciences
- Materials
- Tech Scout
- Unparalleled Data Quality
- Higher Quality Content
- 60% Fewer Hallucinations
Browse by: Latest US Patents, China's latest patents, Technical Efficacy Thesaurus, Application Domain, Technology Topic, Popular Technical Reports.
© 2025 PatSnap. All rights reserved.Legal|Privacy policy|Modern Slavery Act Transparency Statement|Sitemap|About US| Contact US: help@patsnap.com