Prevention of Water and Condensate Blocks in Wells
- Summary
- Abstract
- Description
- Claims
- Application Information
AI Technical Summary
Benefits of technology
Problems solved by technology
Method used
Image
Examples
example 1
[0047] The contact angle test on a core chip was observed using water as the fluid phase, before and after treatment with a wettability modifier (Rhodafac-PA-32®, a linear alcohol ethoxylate phosphate ester, available from Rhodia Inc., Cranbury, N.J., U. S. A.). Before treatment, water spread on the core chip (the contact angle was close to zero) showing that the core was water-wet. After treatment the contact angle was greater than 90° showing that the wettability had been altered to gas wetting.
example 2
[0048]FIG. 3 shows the data from an initial imbibition test on a dry core and then an imbibition test on the same core after treatment with Zonyl 8740®. Zonyl 8740® is an aqueous dispersion containing 30% by weight of a perfluoroalkyl methacrylic copolymer. It is commercially available from DuPont Specialty Chemicals, Wilmington, Del., U. S. A., and is described as being a “waterborne oil and water repellent” material. The y-axis shows the percentage of void volume in the core occupied by water as a function of time. Before treatment, 55% of the void volume was filled with water in less than 50 minutes, showing that the core was water-wet. After treatment with the wettability modifier, the water intake was drastically reduced, showing that the wettability of the core had been changed from water-wet to gas wetting.
example 3
[0049] The contact angle test was performed on a core chip that had been treated with a solution of 5% Zonyl 8740® +93 % water+2% KCl. The contact angle was greater than 90° after the treatment, indicating that the wettability had been altered to gas wetting. The imbibition test data for this fluid system was given in example 2. From the contact angle and imbibition data it can be seen that this system may be used for prevention of water blocks. The contact angle test was also performed on a core chip that had been treated with a dilute solution of Novec® fluorosurfactant FC-4430, available from 3M, Performance Materials Division, St. Paul, Minn., U. S. A. This material is a non-ionic polymeric fluorochemical surfactant (fluoroaliphatic polymeric esters) obtained as a solution that was 2%, in water and methanol, of a mixture that had been 90% active ingredient, 8% non-fluorochemical additives (polyether polymer), and 2% N-methyl-2-pyrrolidone / toluene solvent. From the contact angle ...
PUM
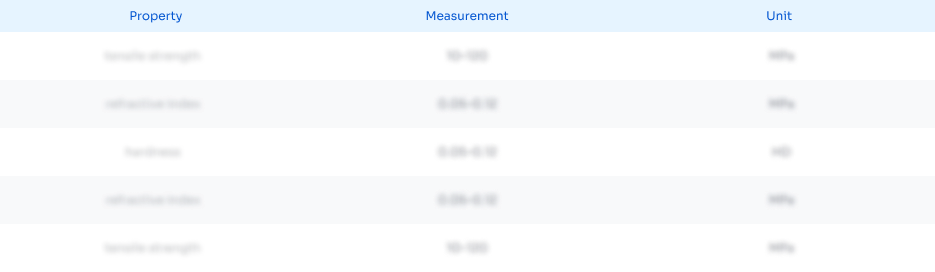
Abstract
Description
Claims
Application Information

- R&D
- Intellectual Property
- Life Sciences
- Materials
- Tech Scout
- Unparalleled Data Quality
- Higher Quality Content
- 60% Fewer Hallucinations
Browse by: Latest US Patents, China's latest patents, Technical Efficacy Thesaurus, Application Domain, Technology Topic, Popular Technical Reports.
© 2025 PatSnap. All rights reserved.Legal|Privacy policy|Modern Slavery Act Transparency Statement|Sitemap|About US| Contact US: help@patsnap.com