Method and apparatus for maskless photolithography
a maskless and photolithography technology, applied in the field of maskless photolithography, can solve the problems of inability to realize the advantages of maskless systems as a result of efficiencies derived from quantities of scale, distortion and uniformity of images, and still arise, so as to achieve efficient pattern creation and easy and quick creation
- Summary
- Abstract
- Description
- Claims
- Application Information
AI Technical Summary
Benefits of technology
Problems solved by technology
Method used
Image
Examples
Embodiment Construction
[0043] References will now be made in detail to the embodiments consistent with the invention, examples of which are illustrated in the accompanying drawings. First, briefly, the invention is a system and method to create two dimensional and three dimensional structures using a maskless photolithography system comprising a maskless pattern generator that is directly reconfigurable and does not require masks, templates or stencils to create each of the planes or layers on a multi layer two-dimensional or three dimensional structure. In an embodiment, the invention uses a micromirror array comprising up to several million elements to modulate light onto a substrate that has photoreactive or photoresist compounds applied to the exposed surface. The desired pattern is designed and stored using conventional computer aided drawing techniques and is used to control the positioning of the individual mirrors in the micromirror array to reflect the corresponding desired pattern. Light impingi...
PUM
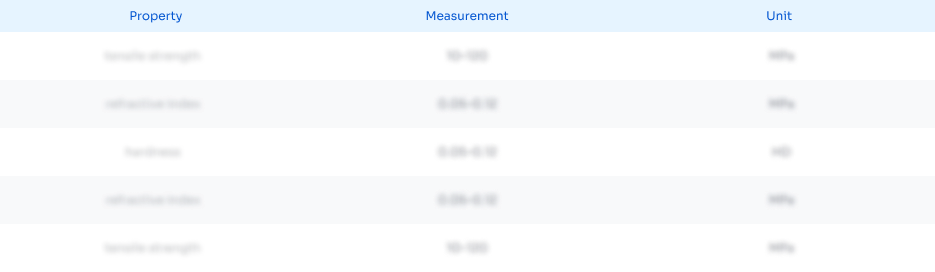
Abstract
Description
Claims
Application Information

- R&D
- Intellectual Property
- Life Sciences
- Materials
- Tech Scout
- Unparalleled Data Quality
- Higher Quality Content
- 60% Fewer Hallucinations
Browse by: Latest US Patents, China's latest patents, Technical Efficacy Thesaurus, Application Domain, Technology Topic, Popular Technical Reports.
© 2025 PatSnap. All rights reserved.Legal|Privacy policy|Modern Slavery Act Transparency Statement|Sitemap|About US| Contact US: help@patsnap.com