Stress bimorph MEMS switches and methods of making same
a technology of rf switch which is applied in the direction of electromagnetic relay, electrical apparatus, capacitor structural combinations, etc., can solve the problems of difficult implementation of rf switch integrated rf switch, poor electrical isolation of switch at high frequencies, and limited distance between metal contact and rf signal line when rf switch is in the open position. , to achieve the effect of reducing off-state capacitance, low actuation voltage, and large separation
- Summary
- Abstract
- Description
- Claims
- Application Information
AI Technical Summary
Benefits of technology
Problems solved by technology
Method used
Image
Examples
Embodiment Construction
[0033] The present disclosure describes a miniature RF switch designed for applications over a frequency range from DC to approximately 100 GHz. The following disclosure describes an RF MEMS switch according to the present invention fabricated on a silicon-based substrate. However, RF MEMS switches according to the present invention may also be fabricated from various other substrate materials, such as gallium arsenide (GaAs), glass, and other dielectrics.
[0034] In a preferred embodiment, a micro-electromechanical switch, generally designated 124 and best illustrated in FIGS. 1, 2 and 3, is fabricated on a substrate 110 using generally known microfabrication techniques, such as masking, etching, deposition, and lift-off. In a preferred embodiment, the RF MEMS switch 124 is directly formed on the substrate 110 and monolithically integrated with a transmission line 114. Alternatively, the RF MEMS switch 124 may be discreetly formed and then bonded to the substrate 110. The switch 124...
PUM
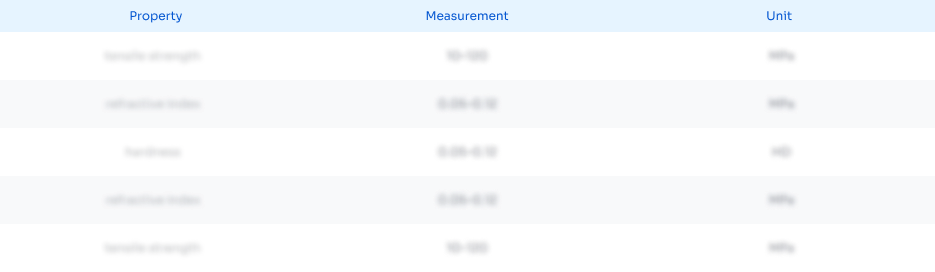
Abstract
Description
Claims
Application Information

- R&D
- Intellectual Property
- Life Sciences
- Materials
- Tech Scout
- Unparalleled Data Quality
- Higher Quality Content
- 60% Fewer Hallucinations
Browse by: Latest US Patents, China's latest patents, Technical Efficacy Thesaurus, Application Domain, Technology Topic, Popular Technical Reports.
© 2025 PatSnap. All rights reserved.Legal|Privacy policy|Modern Slavery Act Transparency Statement|Sitemap|About US| Contact US: help@patsnap.com