Fuel composition
a technology of fuel composition and additives, applied in the field of fuel additives, can solve the problems of affecting affecting the safety of people, so as to improve the chemical reactivity of metals, prevent the access of corrosive components, and reduce or prevent corrosion
- Summary
- Abstract
- Description
- Claims
- Application Information
AI Technical Summary
Benefits of technology
Problems solved by technology
Method used
Image
Examples
examples
Fuel Lubricity Characteristics
[0174] The lubricity of diesel fuel is most conveniently measured by means of the test protocol well known to those skilled in the art as the CEC F-06-A-96 HFRR test. Diesel fuel blends were tested to this method, modified solely in respect of temperature of execution. The standard procedure is executed at 60° C. Because of flash point concerns in blends containing ethanol, the tests were carried out at 25° C. Values for lubricity were established. Some of the diesel fuel blends contained ethanol, together with additional minor components as indicated in the data set contained in Table 2.
TABLE 2Lubricity characteristics of diesel fuels with and without alcoholWear Scar Diameter,Fuel testedmicronsULSD 3258ULSD 3 + Ethanol + Octimax339EN 590237EN 590 + Ethanol + Octimax313Kerosene732Kerosene + Ethanol + Octimax412Kerosene + Ethanol745
[0175] The minor component described as Octimax is a co-solvent [STEVE —is Octimax available from a commercial source? ...
PUM
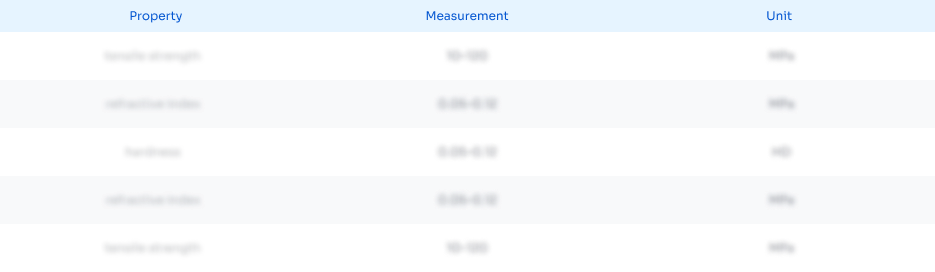
Abstract
Description
Claims
Application Information

- R&D Engineer
- R&D Manager
- IP Professional
- Industry Leading Data Capabilities
- Powerful AI technology
- Patent DNA Extraction
Browse by: Latest US Patents, China's latest patents, Technical Efficacy Thesaurus, Application Domain, Technology Topic, Popular Technical Reports.
© 2024 PatSnap. All rights reserved.Legal|Privacy policy|Modern Slavery Act Transparency Statement|Sitemap|About US| Contact US: help@patsnap.com