Turbocharger
a turbocharger and internal combustion engine technology, applied in the direction of combustion engines, internal combustion piston engines, machines/engines, etc., can solve the problems of limited inlet pressure of si engines, major difficulties that must be overcome, and advanced si engine turbocharging and other problems, to achieve the effect of reducing cost and fast catalyst light-o
- Summary
- Abstract
- Description
- Claims
- Application Information
AI Technical Summary
Benefits of technology
Problems solved by technology
Method used
Image
Examples
Embodiment Construction
[0028] With reference to FIG. 1, an inner ductwork of a jacketed integrated turbocharger / manifold 100 comprises a manifold inlet flange 110, and five primary pipes 111, 112, 113, 114, and 115. Further, it comprises two branched pipes 120, 121, one double-branched pipe 125 consisting of an upper portion 125′ and a lower portion 125″, a first turbine housing portion 130, and a second turbine housing portion 131. The second turbine housing portion includes a waste-gate opening 132. Still further, the inner ductwork of the jacketed integrated turbocharger / manifold 100 comprises a waste-gate duct 140, an exhaust duct 142, and a turbine outlet flange 144, comprising a waste-gate 146. Finally, the inner ductwork of the jacketed integrated turbocharger / manifold 100 includes a bearing housing flange 150.
[0029] In FIG. 2, components constituting an outer housing or shell for the inner ductwork of the jacketed integrated turbocharger / manifold 100 are shown. Those components are a lower outer ...
PUM
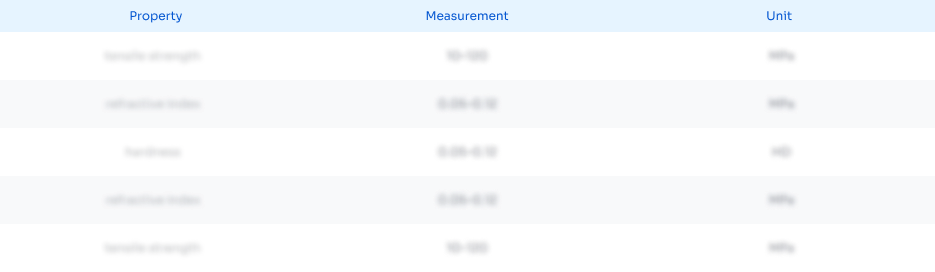
Abstract
Description
Claims
Application Information

- R&D
- Intellectual Property
- Life Sciences
- Materials
- Tech Scout
- Unparalleled Data Quality
- Higher Quality Content
- 60% Fewer Hallucinations
Browse by: Latest US Patents, China's latest patents, Technical Efficacy Thesaurus, Application Domain, Technology Topic, Popular Technical Reports.
© 2025 PatSnap. All rights reserved.Legal|Privacy policy|Modern Slavery Act Transparency Statement|Sitemap|About US| Contact US: help@patsnap.com