Well treatment fluid
- Summary
- Abstract
- Description
- Claims
- Application Information
AI Technical Summary
Benefits of technology
Problems solved by technology
Method used
Image
Examples
example 1
Radial Fluid Loss for Newtonian Fluids
[0043] To demonstrate the effect of increased viscosity on radial fluid loss for a Newtonian fluid, the fluid loss of two solids-free weighted fluids are compared. The viscosity data for weighted fluids, which were used to simulate completion brines, were obtained from Foxenberg, W. E., et al., “Effects on Completion Fluid Loss on Well Productivity”, SPE 31137, presented at the SPE International Symposium on Formation Damage Control 14-15 February 1996, Lafayette, La., USA to be used in Eq. (1) and (2). Viscosity data for weighted fluids solutions other than completion brines were obtained from Perry and Green, Perry's Chemical Engineers' Hand book, 6th edition, 1984, p. 3-251 and 2-352.
[0044] The rate of fluid loss of both types of pills can be approximated by calculating the fluid loss of a Newtonian fluid according to the following Equation (1) as discussed in “Power-Law Flow and Hydrodynamic Behavior of Biopolymer Solutions in Porous Media...
example 2
Radial Fluid Loss for a Glycerol Fluid
[0051] Using the methods described in Example 1, the fluid loss rate for a NaCl brine solution and a polyglycol solution can be compared. For a well formation that has permeability of 10 md, porosity of 0.3, and bottom hole temperature of 425° F. (218° C.), a fluid density of 9.2 ppg (1.1 g / ml) is required to maintain an overbalanced pressure of 300 psig during the completion process. The well that has an interval length of 100 ft. (30 m) and the wellbore radius of 3 inches (7.6 cm), requires 3.5 bbl (556 1) of fluid to fill the wellbore. At 425° F. (218° C.), 10.0 ppg, (1.2 g / ml) NaCl brine has a viscosity of about 0.28 cp and 8.334 ppg (1 g / ml) NaCl brine (less than 10 g / L NaCl) has a viscosity of less than 0.1 cp. Therefore, for a 9.2 ppg (1.1 g / ml) NaCl, a viscosity of 0.2 will be used. The data listed in Table 2 indicates this polyglycol based fluid controls fluid loss much better than the brine. For example, in one hour about 175 bbls (27...
example 3
Viscosity of Polyglycol Fluid with Added Hydroxypropyl Cellulose
[0053] The viscosities of a polyglycol with and without added viscosifying agents were measured and compared. One barrel (159 1) of a polyethylene glycol fluid having an average molecular weight of 200 grains / mole and sold under the trade name Polyglycol E2000 by Dow Chemical, Inc. was admixed with 5 pounds (1.9 kg) hydroxypropyl cellulose (HPC). After mixing for 1 hour at room temperature, the viscosity was measured on a variable speed rheometer at 120° F. (49° C.) and 180° F. (82° C.) under a wide range of shear conditions. The results of the viscosity measurements for both the polyglycol fluid and the polyglycol fluid with added HPC are listed in Table 3. Analysis of the results underscores the enhanced viscosity that can be achieved by the addition of a viscosifying agent. The fluids prepared according to this invention demonstrate non-Newtonian characteristics. These fluids exhibit increased viscosity at low shear...
PUM
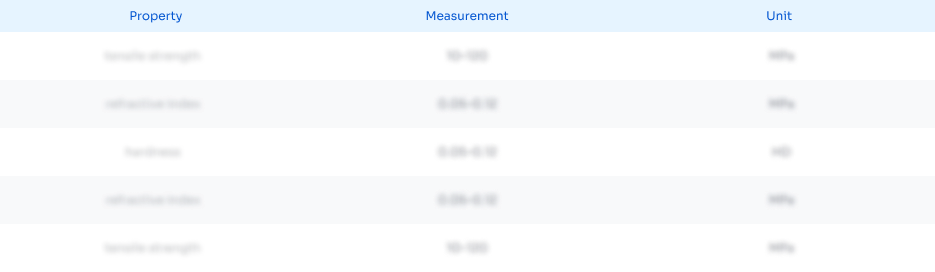
Abstract
Description
Claims
Application Information

- R&D
- Intellectual Property
- Life Sciences
- Materials
- Tech Scout
- Unparalleled Data Quality
- Higher Quality Content
- 60% Fewer Hallucinations
Browse by: Latest US Patents, China's latest patents, Technical Efficacy Thesaurus, Application Domain, Technology Topic, Popular Technical Reports.
© 2025 PatSnap. All rights reserved.Legal|Privacy policy|Modern Slavery Act Transparency Statement|Sitemap|About US| Contact US: help@patsnap.com