Systems and methods for forming blister packages with support members for pharmaceutical product packaging
- Summary
- Abstract
- Description
- Claims
- Application Information
AI Technical Summary
Benefits of technology
Problems solved by technology
Method used
Image
Examples
Embodiment Construction
[0035] FIG. 1 illustrates a top plan view of the finished blister pack formed in accordance with an exemplary embodiment of the present invention that is shown generally at 10. The overall package is comprised of a support member 12 that incorporates a plurality of openings 14 for receiving individual doses of solid pharmaceutical products 16. The solid pharmaceutical products are secured via a clear plastic material 18. This material is preferably thermoplastic material such as polyethylene but other suitable plastic materials will also perform satisfactory results. In a preferred exemplary embodiment, polyethylene co-extruded with saran or other clear plastic material may be utilized. The most preferred material is medical packaging film manufactured by Dow Chemical Corporation known as MPF 2005 or Saranex which is readily available.
[0036] The product displayed in FIGS. 1 and 2 represents the overall finished product that is formed in the manufacturing process described below. FIG...
PUM
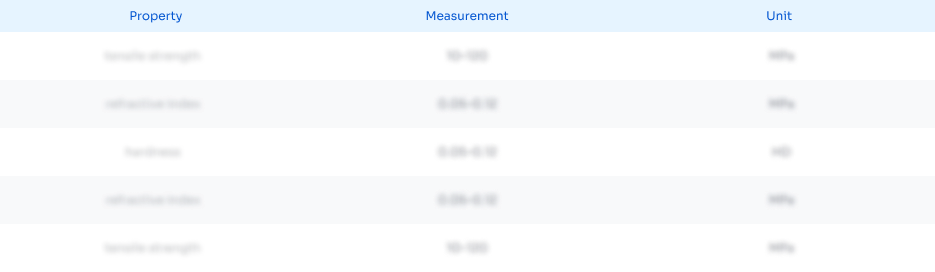
Abstract
Description
Claims
Application Information

- R&D
- Intellectual Property
- Life Sciences
- Materials
- Tech Scout
- Unparalleled Data Quality
- Higher Quality Content
- 60% Fewer Hallucinations
Browse by: Latest US Patents, China's latest patents, Technical Efficacy Thesaurus, Application Domain, Technology Topic, Popular Technical Reports.
© 2025 PatSnap. All rights reserved.Legal|Privacy policy|Modern Slavery Act Transparency Statement|Sitemap|About US| Contact US: help@patsnap.com