Process and apparatus for eliminating fume SO2 from waste coking ammonia water of iron and steel and coal chemical enterprise
A technology of SO2 and ammonia water, applied in chemical instruments and methods, separation of dispersed particles, separation methods, etc., can solve the problems of large investment and achieve the effects of improving economic benefits, reducing energy consumption, and reducing production costs
- Summary
- Abstract
- Description
- Claims
- Application Information
AI Technical Summary
Problems solved by technology
Method used
Image
Examples
Embodiment 1
[0017] Directly use 2% low-concentration waste ammonia water produced by coking as the ammonia source of the absorbent for sintering flue gas or coal-fired boiler flue gas SO 2 The removal of Fe +3 , After the treatment, the flue gas is discharged up to the standard, and the ammonium sulfate is recovered. The specific process is as follows:
[0018] 1. Hot flue gas or boiler flue gas from steel sintering at 130°C (SO 2 Concentration 1000mg-2000mg / Nm 3 , Dust 3 , has been electrostatically precipitated or bagged), and enters the reverse nozzle of the flue gas cooling and mother liquor concentration tower (7) from the upper part at a gas velocity of 20m / s. 3 Ammonium sulfate salt solution, the liquid-gas volume ratio L / G is 3 / 1000, after adiabatically cooling to 50°C in the turbulent flow reverse spray tower, the flue gas is discharged from the top of the flue gas cooling and mother liquor concentration tower (7) and discharged at a distance of 20m / s gas velocity enters the...
Embodiment 2
[0022] Directly use 10% low-concentration waste ammonia water produced by coking as the ammonia source of the absorbent for sintering flue gas or coal-fired boiler flue gas SO 2 removal; S 2 o 3 -2 , After the treatment, the flue gas is discharged up to the standard, and the ammonium sulfate is recovered. The specific process is as follows:
[0023] 1. Hot flue gas or boiler flue gas from steel sintering at 140°C (SO 2 Concentration 2000mg-5000mg / Nm 3 , Dust 3 , has been electrostatically precipitated or bagged), and enters the reverse nozzle of the flue gas cooling and mother liquor concentration tower (7) from the upper part at a gas velocity of 22m / s. 3 ammonium sulfate solution, the liquid-gas volume ratio L / G is 3 / 1000, after adiabatically cooling to 60°C in the turbulent reverse spray tower, the flue gas is discharged from the top of the flue gas cooling and mother liquor concentrating tower (7) and discharged at 23m / s gas velocity enters the upper reverse nozzle ...
Embodiment 3
[0027] Directly use 20% low-concentration waste ammonia water produced by coking as the ammonia source of the absorbent for sintering flue gas or coal-fired boiler flue gas SO 2 The removal of Fe +3 , After the treatment, the flue gas is discharged up to the standard, and the ammonium sulfate is recovered. The specific process is as follows:
[0028] 1. Hot flue gas or boiler flue gas from steel sintering at 150°C (SO 2 Concentration 3000mg-5000mg / Nm 3 , Dust 3 , has been electrostatically precipitated or bagged), and enters the reverse nozzle of the flue gas cooling and mother liquor concentration tower (7) from the upper part at a gas velocity of 27m / s, and the lower part of the reverse nozzle is sprayed upwards by the nozzle at 50°C and a density of 1230g / m3 3 Ammonium sulfate salt solution, the liquid-gas volume ratio L / G is 3 / 1000, after being adiabatically cooled to 65°C in the turbulent flow reverse spray tower, the flue gas is discharged from the top of the flue gas...
PUM
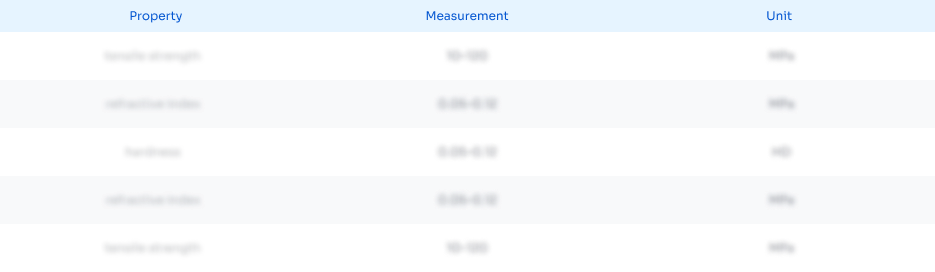
Abstract
Description
Claims
Application Information

- R&D
- Intellectual Property
- Life Sciences
- Materials
- Tech Scout
- Unparalleled Data Quality
- Higher Quality Content
- 60% Fewer Hallucinations
Browse by: Latest US Patents, China's latest patents, Technical Efficacy Thesaurus, Application Domain, Technology Topic, Popular Technical Reports.
© 2025 PatSnap. All rights reserved.Legal|Privacy policy|Modern Slavery Act Transparency Statement|Sitemap|About US| Contact US: help@patsnap.com