Polymer light-emitting-diode making method
A technology of light-emitting diodes and manufacturing methods, which is applied in semiconductor/solid-state device manufacturing, electrical components, electric solid-state devices, etc., can solve the problems of low luminous purity of polymer light-emitting diodes, and achieve the effect of improving luminous purity
- Summary
- Abstract
- Description
- Claims
- Application Information
AI Technical Summary
Problems solved by technology
Method used
Image
Examples
Embodiment Construction
[0013] Please refer to FIG. 2 , which is a flow chart of a preferred embodiment of the manufacturing method of the polymer light emitting diode of the present invention. The manufacturing method of the polymer light-emitting diode comprises the following steps: providing a base; forming an anode layer on the base; forming a polymer light-emitting layer on the anode layer; ultrasonically treating the polymer light-emitting layer; baking the polymer light-emitting layer ; Sealing the polymer light-emitting layer. details as follows:
[0014] (1) Provide a base
[0015] The substrate acts as a carrier for other components, and its material is usually glass, organic film or plastic.
[0016] (2) Forming the anode layer
[0017] The anode layer is formed on the substrate. The anode layer may be a transparent conductive material, such as indium tin oxide (ITO) or indium zinc oxide (IZO), or a thin metal conductive film through which light can pass. The anode layer can be formed...
PUM
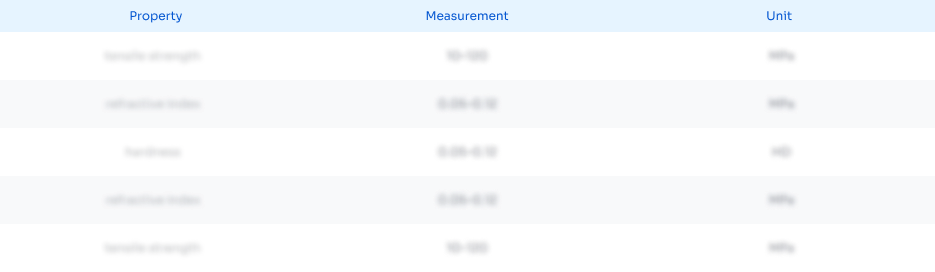
Abstract
Description
Claims
Application Information

- Generate Ideas
- Intellectual Property
- Life Sciences
- Materials
- Tech Scout
- Unparalleled Data Quality
- Higher Quality Content
- 60% Fewer Hallucinations
Browse by: Latest US Patents, China's latest patents, Technical Efficacy Thesaurus, Application Domain, Technology Topic, Popular Technical Reports.
© 2025 PatSnap. All rights reserved.Legal|Privacy policy|Modern Slavery Act Transparency Statement|Sitemap|About US| Contact US: help@patsnap.com