Metal materials protection method (1)
A metal material and metal matrix technology, applied in the field of material science, can solve the problems affecting the bonding strength of the coating and the matrix, the large difference in thermal expansion coefficient, and the low bonding strength, so as to achieve good oxidation resistance, high bonding strength, and improve comprehensive performance. Effect
- Summary
- Abstract
- Description
- Claims
- Application Information
AI Technical Summary
Problems solved by technology
Method used
Image
Examples
Embodiment 1
[0037] 1Cr11Ni2W2MoV stainless steel, after surface pre-grinding, polishing, decontamination, acetone ultrasonic cleaning. After the furnace is installed, the background vacuum is pumped to 6.0×10 -3 Pa, heated to the substrate temperature to 300°C, the sample is rotated at 60r / min in front of the Ti target, and Ar is introduced to 0.06Pa, and the negative peak value is -1000V, the pulse width is 20,000Hz, and the duty cycle is 30%. Turn on the Ti target under bias to bombard the cleaned sample for 3 min. During the bombardment, the arc voltage was 16-19V, and the arc current was 60A.
[0038] into Ar and N 2 The mixed gas to 1Pa, where N 2The partial pressure is about 0.6Pa. Using unipolar pulse bias, adjust the negative peak value to 600V, the pulse width to 20,000 Hz, and the duty cycle to 30%; the sample is rotated at 60r / min in front of the Ti target, the Ti target is opened to deposit the TiN bottom layer, and the arc current is 60A. The time is 10 minutes; start th...
Embodiment 2
[0048] 1Cr11Ni2W2MoV stainless steel, after surface pre-grinding, polishing, decontamination, acetone ultrasonic cleaning. After the furnace is installed, the background vacuum is pumped to 6.0×10 -3 Pa, heated to the substrate temperature to 300°C, the sample is rotated at 100r / min in front of the Ti target, and Ar is passed through to 0.06Pa, and the negative peak value is -1000V, the pulse width is 20,000Hz, and the duty cycle is 30%. Turn on the Ti target under bias to bombard the cleaned sample for 3 min. During the bombardment, the arc voltage was 16-19V, and the arc current was 60A.
[0049] into Ar and N 2 The mixed gas to 1Pa, where N 2 The partial pressure is 0.6Pa. Using unipolar pulse bias, adjust the negative peak value to 600V, the pulse width to 20,000Hz, and the duty cycle to 30%; the sample is rotated at 200r / min in front of the Ti target, and the TiAl target with an Al content of 30% is used to deposit the TiN bottom layer. The arc current is 250A, and t...
Embodiment 3
[0051] 1Cr11Ni2W2MoV stainless steel, after surface pre-grinding, polishing, decontamination, acetone ultrasonic cleaning. After the furnace is installed, the background vacuum is pumped to 6.0×10 -3 Pa, heated to the substrate temperature to 300°C, the sample is rotated at 80r / min in front of the Ti target, and Ar is passed through to 0.06Pa, the negative peak value is -1000V, the pulse width is 20,000Hz, and the duty cycle is 30% pulse Turn on the Ti target under bias to bombard the cleaned sample for 3 min. During the bombardment, the arc voltage was 16-19V, and the arc current was 60A.
[0052] into Ar and N 2 The mixed gas to 1Pa, where N 2 The partial pressure is 0.6Pa. Using unipolar pulse bias, adjust the negative peak value to 600V, the pulse width to 20,000Hz, and the duty cycle to 30%; the sample is rotated at 5r / min in front of the Ti target, and the TiAl target with an Al content of 5% is used to deposit the TiN bottom layer. The arc current is 10A, and the t...
PUM
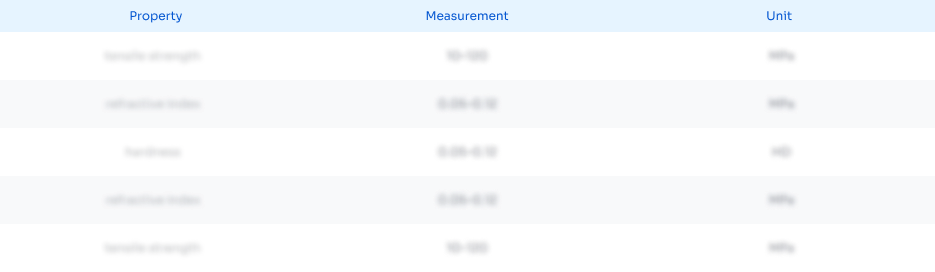
Abstract
Description
Claims
Application Information

- R&D
- Intellectual Property
- Life Sciences
- Materials
- Tech Scout
- Unparalleled Data Quality
- Higher Quality Content
- 60% Fewer Hallucinations
Browse by: Latest US Patents, China's latest patents, Technical Efficacy Thesaurus, Application Domain, Technology Topic, Popular Technical Reports.
© 2025 PatSnap. All rights reserved.Legal|Privacy policy|Modern Slavery Act Transparency Statement|Sitemap|About US| Contact US: help@patsnap.com