Binding method for magnetic material before inner-round dissection
A magnetic material and circular cutting technology, which is applied in the manufacture of inductors/transformers/magnets, electrical components, circuits, etc., can solve the problems of unfavorable product whole board inspection, chip dropping, loose and loose, etc., to achieve tight combination, not easy to drop chips, The effect of reducing the likelihood
- Summary
- Abstract
- Description
- Claims
- Application Information
AI Technical Summary
Problems solved by technology
Method used
Examples
Embodiment 1
[0013] The D11*28 cylindrical magnets to be cut are respectively selected with surface-treated and untreated materials, soaked in pure diesel oil, wiped clean, and then directly use 502 according to 6-5-6-5-4 ( A total of 26) are arranged for bonding. Thereafter, the bonded magnet is processed to a thickness of 1.5 mm. Results There was no chip falling during the cutting process, and the bonded whole board was not scattered. The bonding strength of the cut whole board was close to that of conventional bonding diesel cutting. The results of the untreated surface and the surface treated surface are the same, and there is no difference.
Embodiment 2
[0015] Soak the D11*28 cylindrical magnets to be cut and processed in pure diesel oil, wipe them clean, and then use 502 to bond them in an arrangement of 6-5-6-5-4 per layer (26 pieces in total). Thereafter, the bonded magnet is processed to a thickness of 1.5 mm. Results There was no chip falling during the cutting process, and the bonded whole board was not scattered. The bonding strength of the cut whole board was close to that of conventional bonding diesel cutting.
Embodiment 3
[0017] Soak the D11*28 cylindrical magnets to be cut in kerosene saturated with chlorinated paraffin, wipe them clean, and then use 502 to arrange them in the order of 6-5-6-5-4 per layer (26 in total) Do the bonding. Thereafter, the bonded magnet is processed to a thickness of 1.5 mm. Results There was no chip falling during the cutting process, and the bonded whole board was not scattered. The bonding strength of the cut whole board was close to that of conventional bonding diesel cutting.
PUM
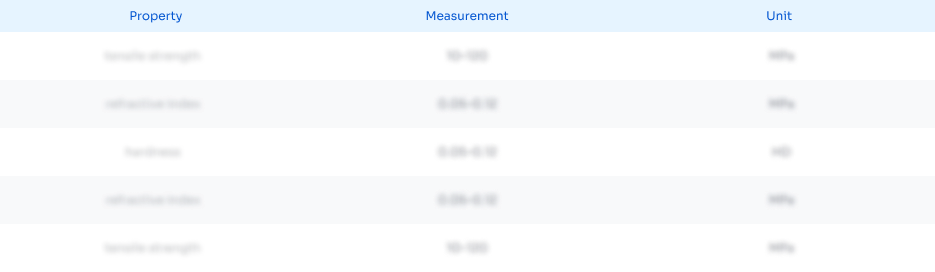
Abstract
Description
Claims
Application Information

- Generate Ideas
- Intellectual Property
- Life Sciences
- Materials
- Tech Scout
- Unparalleled Data Quality
- Higher Quality Content
- 60% Fewer Hallucinations
Browse by: Latest US Patents, China's latest patents, Technical Efficacy Thesaurus, Application Domain, Technology Topic, Popular Technical Reports.
© 2025 PatSnap. All rights reserved.Legal|Privacy policy|Modern Slavery Act Transparency Statement|Sitemap|About US| Contact US: help@patsnap.com