Catalytic oxidation process for treating tail gas from absorption tower of acrylonitrile installation
A catalytic oxidation and treatment process technology, applied in the chemical industry, organic chemistry, climate sustainability, etc., can solve the problems of high operating costs, large incineration exhaust, large fuel, etc., to achieve a wide operating range and thorough tail gas treatment , long service life effect
- Summary
- Abstract
- Description
- Claims
- Application Information
AI Technical Summary
Problems solved by technology
Method used
Image
Examples
Embodiment Construction
[0020] The process of the present invention will be further described below in conjunction with the accompanying drawings and embodiments.
[0021] Such as figure 1 and 2 As shown, the first embodiment of the present invention provides a catalytic oxidation treatment process for the tail gas of the absorption tower of an acrylonitrile plant.
[0022] In the start-up stage, after the fuel gas and air are mixed, they are heated to the ignition temperature of the catalyst by the electric heater or steam heater 1, and then enter the catalytic reactor 2 for catalytic oxidation reaction. Gradually switch the tail gas of the absorption tower into the catalytic reactor 2, switch the fuel out of the catalytic reactor 2, fix the honeycomb ceramic catalyst on the catalyst fixed bed 15, and keep the internal pressure of the catalytic reactor 2 at about 7.5kPa and the temperature at about 400°C , the above-mentioned absorption tower tail gas and air or oxygen carry out catalytic oxidatio...
PUM
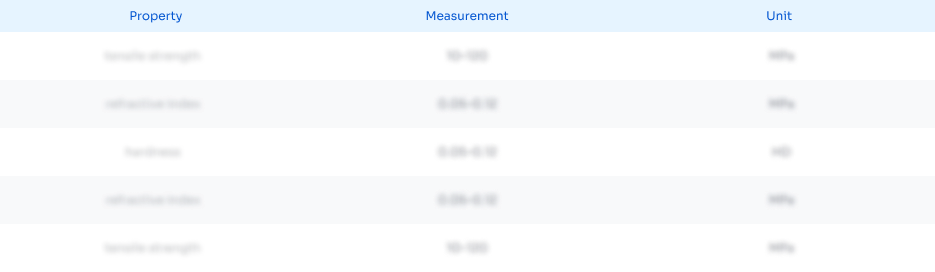
Abstract
Description
Claims
Application Information

- R&D Engineer
- R&D Manager
- IP Professional
- Industry Leading Data Capabilities
- Powerful AI technology
- Patent DNA Extraction
Browse by: Latest US Patents, China's latest patents, Technical Efficacy Thesaurus, Application Domain, Technology Topic, Popular Technical Reports.
© 2024 PatSnap. All rights reserved.Legal|Privacy policy|Modern Slavery Act Transparency Statement|Sitemap|About US| Contact US: help@patsnap.com