Method for improving critical current density of Bi-2223 strip material
A bi-2223, critical current technology, applied in the usage of superconductor elements, circuits, electrical components, etc., can solve problems such as no substantial progress, and achieve the effect of improving performance
- Summary
- Abstract
- Description
- Claims
- Application Information
AI Technical Summary
Problems solved by technology
Method used
Image
Examples
Embodiment
[0017] 1. First carefully polish off the insulating varnish on the selected area (edge part) of the strip with finer sandpaper, and clean the surface of the strip; select a DC stabilized power supply as the electroplating power supply, and the output voltage of the power supply is 3V. Strip current 30mA. The thickness of the coating on the surface of the composite wire is changed by changing the electroplating time. The electroplating time is chosen as 30~180 minutes, obtains the Bi-2223 strip material of electroplating ferromagnetic material on the surface, as figure 1 As shown in the figure, the surface of the superconducting layer 3 is covered with a silver layer 2, and the outer surface of the silver layer 2 is a ferromagnetic coating 1. Wherein the electroplating solution for electroplating ferromagnetic material is 50wt% NiSO by volume 4 : 50wt% NiCl 2 : 3g / 100ml of HBO 3 = 1:1:1 dubbed.
[0018] 2. In the electroplating process, we have selected different coating...
PUM
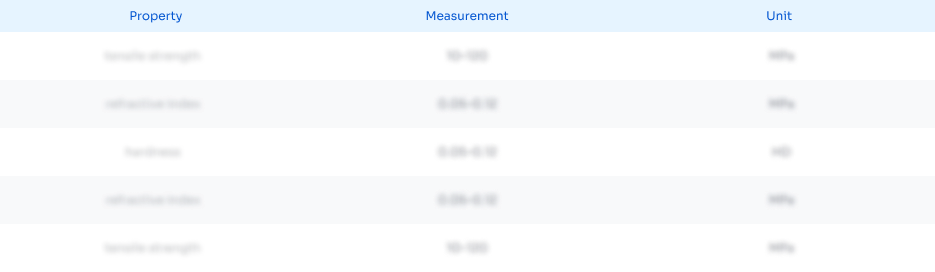
Abstract
Description
Claims
Application Information

- Generate Ideas
- Intellectual Property
- Life Sciences
- Materials
- Tech Scout
- Unparalleled Data Quality
- Higher Quality Content
- 60% Fewer Hallucinations
Browse by: Latest US Patents, China's latest patents, Technical Efficacy Thesaurus, Application Domain, Technology Topic, Popular Technical Reports.
© 2025 PatSnap. All rights reserved.Legal|Privacy policy|Modern Slavery Act Transparency Statement|Sitemap|About US| Contact US: help@patsnap.com