Micro photo-electro-mechanical gyro
A micro-optical electromechanical and gyroscope technology is applied in the direction of rotating gyroscope, gyroscopic effect for speed measurement, microstructure technology, etc. It can solve the problems of expensive equipment, inability to improve detection accuracy, and difficulty in processing suspension structures
- Summary
- Abstract
- Description
- Claims
- Application Information
AI Technical Summary
Problems solved by technology
Method used
Image
Examples
Embodiment Construction
[0039]As can be seen from the figure, the entire micro-opto-electromechanical gyroscope system is composed of an optical reader, a surface acoustic wave sensor and a signal processing system: the optical waveguide reader is composed of a laser light source 1, a light source drive circuit 9, an electro-optical waveguide modulator 3 and a photoelectric The detector 2 is composed; the surface acoustic wave sensor is composed of an acoustic wave drive circuit 8 and an interdigital transducer (IDT); the signal processing system 7 still adopts an electrical signal processing method. The entire micro-opto-electromechanical gyroscope system is integrated on an integrated chip with lithium niobate crystal as the substrate material 6, and the substrate size is 20×10×1mm. A semiconductor laser 1 (FLMM-0808-7*1-1.5W) with a wavelength of λ=808nm is driven by a light source drive circuit 9, and is bonded to a photodetector 2 (PIN21112) at both ends of an optical waveguide 4 with a central w...
PUM
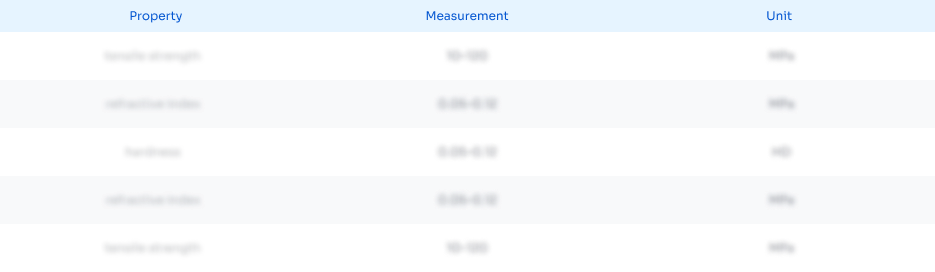
Abstract
Description
Claims
Application Information

- R&D
- Intellectual Property
- Life Sciences
- Materials
- Tech Scout
- Unparalleled Data Quality
- Higher Quality Content
- 60% Fewer Hallucinations
Browse by: Latest US Patents, China's latest patents, Technical Efficacy Thesaurus, Application Domain, Technology Topic, Popular Technical Reports.
© 2025 PatSnap. All rights reserved.Legal|Privacy policy|Modern Slavery Act Transparency Statement|Sitemap|About US| Contact US: help@patsnap.com