Method of manufacturing release film
A production method and release film technology, applied in the direction of layered products, etc., can solve the problems of reducing the qualified rate, increasing the production cost, and high cost, and achieving the effects of uniform material thickness, convenient process, and improved processing rate.
- Summary
- Abstract
- Description
- Claims
- Application Information
AI Technical Summary
Problems solved by technology
Method used
Image
Examples
no. 1 example
[0092] Use KBOPP / AC / PE coating and KPET / AC / PE coating as two release film substrates, and use Shin-Etsu's solvent-based silicone release agent KS-3703 / KS-3800 Toluene is used as a solvent, and after mixing in a ratio of 3:1, 2% CAT-PL-50T platinum catalyst is added, and the prepared release agent toluene solution is coated on the above-mentioned release film substrate with a No. 8 wire rod PE coating surface, KBOPP and KPET surface, the coating surface is corona treatment surface, and dry in a hot air circulation oven at 100°C for 1 minute as the curing and drying condition of the release agent, the coating amount of Silicone is 0.8 g / m2 , placed in an environment with a relative humidity of 60% and a temperature of 25°C for one day, stick a one-inch-wide Tesa7475 tape on the release agent coated surface, and use double-sided tape to seal the non-release agent of the release film The coated surface is pasted on the stainless steel sheet, and rolled twice with a 2 kg rubber whe...
no. 2 example
[0099] Take KBOPP / AC / PE coating and KPET / AC / PE coating two release film substrates, use Shin-Etsu's low-temperature bridging solvent-type silicone release agent solution, KS -847T as the main agent, toluene as the solvent, after mixing, add 2% CAT-PL-50T platinum catalyst, and use No. PE coating surface, KBOPP and KPET surface, the coating surface is corona treatment surface, and the release agent is cured and dried in a hot air circulation oven at 90°C for 1 minute. The coating amount of Silicone is 0.7 g / m2. After being placed in an environment with a relative humidity of 60% and a temperature of 25°C for one day, stick a one-inch-wide Tesa7475 tape on the release agent coated surface, and use the double-sided tape to coat the non-release agent of the release film. The cloth surface is pasted on the stainless steel sheet, and the rubber wheel with a weight of 2 kg is rolled back and forth twice, and then the peeling force is measured after 0, 1 and 7 days under the pressure ...
no. 3 example
[0106] Take KBOPP / AC / PE coating and KPET / AC / PE coating two release film substrates, with weight percent as 1% polyvinyl octadecyl carbamate (Polyvinyl Octadecyl Carbamate, one party company oil industry Co., Ltd. Co., Ltd. Peeloil 1010) non-silicon Likang off-toluene solution, coated with 0.07 g / m2 by 150-mesh gravure printing, coated on the PE coating surface, KBOPP and KPET surface of the above-mentioned release film substrate, the coated surface is Corona-treated surface, and dried in a hot air circulation oven at 100°C for 1 minute, placed in an environment with a relative humidity of 60% and a temperature of 25°C for one day, tested the tape and WQ4012 rubber with a one-inch-wide Tesa7475 acrylic tape The tape is pasted on the release agent coated surface of each release film. According to the PSTC-6 test method, use a universal tensile testing machine at a peeling angle of 180°, and peel off at 0.3 m / min and 50 m / min respectively. Speed pull test the release force of t...
PUM
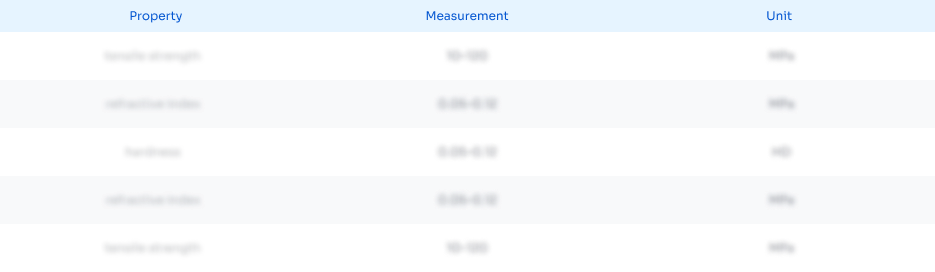
Abstract
Description
Claims
Application Information

- Generate Ideas
- Intellectual Property
- Life Sciences
- Materials
- Tech Scout
- Unparalleled Data Quality
- Higher Quality Content
- 60% Fewer Hallucinations
Browse by: Latest US Patents, China's latest patents, Technical Efficacy Thesaurus, Application Domain, Technology Topic, Popular Technical Reports.
© 2025 PatSnap. All rights reserved.Legal|Privacy policy|Modern Slavery Act Transparency Statement|Sitemap|About US| Contact US: help@patsnap.com