Preparation process for disk type brake lining and dedicated apparatus therefor
A technology of disc brake pads and special equipment, applied in mechanical equipment, friction linings, etc., can solve problems such as uneven thermal stress distribution of brake pads, large temperature gradient, expansion and cracking of brake pads, and achieve a heating and curing process Continuous, uniform distribution of thermal stress, avoid expansion and cracking effect
- Summary
- Abstract
- Description
- Claims
- Application Information
AI Technical Summary
Problems solved by technology
Method used
Image
Examples
Embodiment Construction
[0024] Below in conjunction with accompanying drawing, the preparation process and special equipment of the disc brake pad provided by the present invention are described in further detail:
[0025] Such as figure 1 and figure 2 Shown are the structural schematic diagram of the forming mechanism and the structural schematic diagram of the mold used in the cold press forming process in the preparation process of the disc brake pad. That is, the cold press forming mechanism includes a press mechanism 1 provided with two (can be 1 or more) upper molds 2 and a platform 4 provided with a positioning mechanism and used to fix a displaceable lower mold 3 corresponding to the upper mold 2 , the platform 4 is provided with a mold hole 5 corresponding to the mold cavity 6 of the lower mold.
[0026] Such as image 3 and Figure 4 Shown are the structural schematic diagram of the vulcanization mechanism and the structural schematic diagram of the vulcanization mechanism mold used in...
PUM
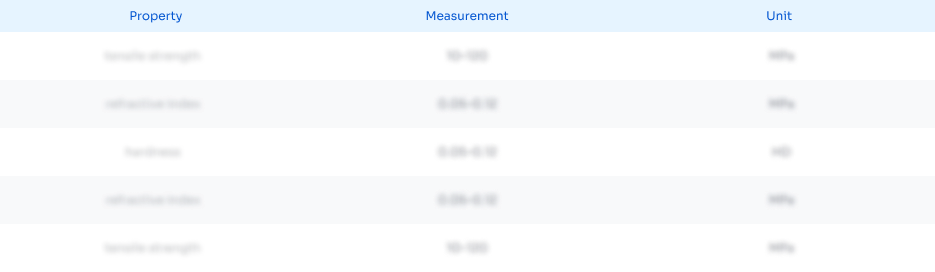
Abstract
Description
Claims
Application Information

- R&D
- Intellectual Property
- Life Sciences
- Materials
- Tech Scout
- Unparalleled Data Quality
- Higher Quality Content
- 60% Fewer Hallucinations
Browse by: Latest US Patents, China's latest patents, Technical Efficacy Thesaurus, Application Domain, Technology Topic, Popular Technical Reports.
© 2025 PatSnap. All rights reserved.Legal|Privacy policy|Modern Slavery Act Transparency Statement|Sitemap|About US| Contact US: help@patsnap.com