Commercial producing method for poly aromatic ether nitrile high molecular halogen-free fire retardant
A technology of nitrile polymers and production methods, which is applied in the direction of fire-resistant coatings, etc., can solve problems such as poor temperature resistance, affecting processing performance, and low production volume proportion, and achieve excellent heat aging resistance, flame retardancy, and processing performance. Good results
- Summary
- Abstract
- Description
- Claims
- Application Information
AI Technical Summary
Problems solved by technology
Method used
Examples
Embodiment Construction
[0012] 1. Mix 400kg of 2,6-dichlorobenzonitrile, 200-300kg of polyphenols, and 300-350kg of polyols in sequence, and then put them into the reactor. The reaction temperature is controlled at 300-350°C, and the pressure is controlled at 2.0-2.5Mpa to carry out the whole reaction process from hydroxylation, esterification to polymerization. After the reaction time is controlled within 6-10 hours, the material is discharged, and the polyarylether nitrile polymer is obtained.
[0013] 2. Cool the reaction mixture to normal temperature, wash with water, separate and dry to obtain a polyarylether nitrile polymer.
[0014] 3. Pulverize the polyarylether nitrile polymer pulverizer, and the fineness is controlled between 80 and 200 mesh.
[0015] 4. Mix 70 kg of crushed polyarylether nitrile polymer with 30 kg of antimony trioxide, then granulate and pack to make 100 kg of polyarylether nitrile high-efficiency halogen-free flame retardant.
PUM
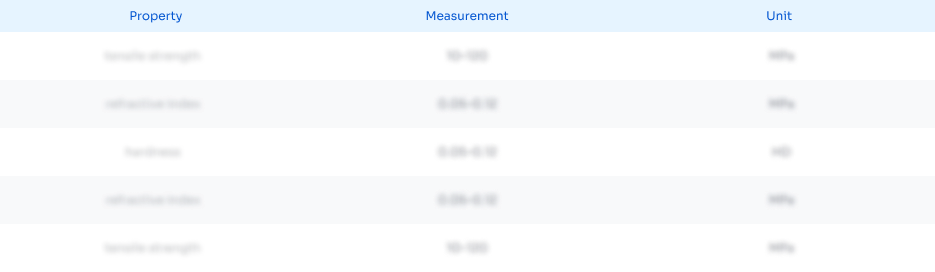
Abstract
Description
Claims
Application Information

- Generate Ideas
- Intellectual Property
- Life Sciences
- Materials
- Tech Scout
- Unparalleled Data Quality
- Higher Quality Content
- 60% Fewer Hallucinations
Browse by: Latest US Patents, China's latest patents, Technical Efficacy Thesaurus, Application Domain, Technology Topic, Popular Technical Reports.
© 2025 PatSnap. All rights reserved.Legal|Privacy policy|Modern Slavery Act Transparency Statement|Sitemap|About US| Contact US: help@patsnap.com