Catalyst active constituent and catalyst containing same
A technology for active components and catalysts, applied in the field of catalyst active components and catalysts, can solve the problems of inability to make dry content, slow catalyst sedimentation, fine catalyst particles, etc., and achieve shortened preparation period, large catalyst particles, and fast sedimentation speed. Effect
- Summary
- Abstract
- Description
- Claims
- Application Information
AI Technical Summary
Problems solved by technology
Method used
Examples
Embodiment 1
[0030] Put 4.76 grams (0.05mol) MgCl 2 , 100mL of decane and 31mL of isooctyl alcohol (0.2mol), heated to 130°C for 180 minutes, cooled to 50°C, at this temperature, 1.1mL of tetraethoxysilane was added to continue the reaction for 60 minutes, and then cooled to room temperature. Add 50mL TiCl slowly over 90 minutes at 0℃ 4In the mixed solution, add 25 mL of chlorocyclohexane after the dripping is completed and slowly raise the temperature to 110°C for 120 minutes and react for 120 minutes to obtain a solid catalyst. After the stirring is stopped, the solid catalyst particles are found to settle quickly. After the reaction, the solid catalyst was filtered out hot. Wash with hexane, 40mL each time, until the filtrate is basically colorless, in which the free titanium content is less than 0.3mg / mL, and the solid catalyst is obtained after drying. The titanium content is 5.92wt%, the Mg content is 17.4wt%, and the Cl content is 63.5 wt%.
Embodiment 2
[0032] Put 5.7 grams (0.05mol) Mg(OEt) 2 , 100mL of decane and 31mL of butanol (0.2mol), heated to 130°C and reacted for 180 minutes, then cooled to 50°C, at this temperature, 1.1mL of tetrabutoxysilane was added to continue the reaction for 60 minutes, and then cooled to room temperature. Slowly add 50 mL of tetraethoxy titanium to the mixed solution at 0°C for 90 minutes. After the addition is complete, add 25 mL of 1,2-dichloroethane and slowly increase the temperature to 110°C for 120 minutes and react for 120 minutes to obtain a solid. For the catalyst, after stopping stirring, the solid catalyst particles will settle faster. After the reaction, the solid catalyst was filtered out hot. Wash with hexane, 40mL each time, until the filtrate is basically colorless, in which the free titanium content is less than 0.3mg / mL, and the solid catalyst is obtained after drying. The titanium content is 5.87wt%, the Mg content is 16.8wt%, and the Cl content is 62.8 wt%.
Embodiment 3
[0034] Put 4.76 g (0.05mol) MgCl 2 , 100mL of decane and 18.3mL of isooctyl alcohol (0.2mol), heated to 130°C for 180 minutes, cooled to 50°C, at this temperature, 1.1mL of tetraethoxysilane was added to continue the reaction for 60 minutes, and then cooled to room temperature. Add 50mL TiCl slowly over 90 minutes at 0℃ 4 In the mixed solution, add 25 mL of chlorocyclohexane after the dripping is completed and slowly raise the temperature to 110°C for 120 minutes and react for 120 minutes to obtain a solid catalyst. After the stirring is stopped, the solid catalyst particles are found to settle quickly. After the reaction, the solid catalyst was filtered out hot. Wash with hexane, 40mL each time, until the filtrate is basically colorless, in which the free titanium content is less than 0.3mg / mL, and the solid catalyst is obtained after drying. The titanium content is 6.02wt%, the Mg content is 17.1wt%, and the Cl content is 64.3 wt%.
PUM
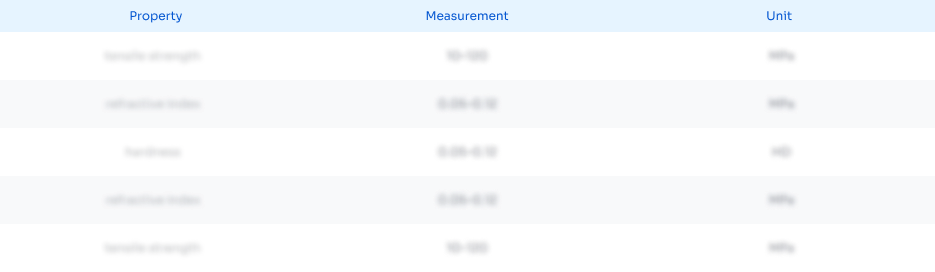
Abstract
Description
Claims
Application Information

- R&D
- Intellectual Property
- Life Sciences
- Materials
- Tech Scout
- Unparalleled Data Quality
- Higher Quality Content
- 60% Fewer Hallucinations
Browse by: Latest US Patents, China's latest patents, Technical Efficacy Thesaurus, Application Domain, Technology Topic, Popular Technical Reports.
© 2025 PatSnap. All rights reserved.Legal|Privacy policy|Modern Slavery Act Transparency Statement|Sitemap|About US| Contact US: help@patsnap.com