Method for reclaiming and cyclic utilizing residue molten steel slag in steel making
A steel slag recovery and waste heat technology, which is applied in the direction of recycling technology, process efficiency improvement, blast furnace parts, etc., can solve the problems of insufficient desulfurization and deoxidation capabilities, insufficient use of heat, and environmental pollution caused by waste steel slag. Achieve the effects of improving the fluidity of slag, satisfying fast-paced production, and reducing production costs
- Summary
- Abstract
- Description
- Claims
- Application Information
AI Technical Summary
Problems solved by technology
Method used
Image
Examples
Embodiment Construction
[0025] This embodiment is a method for heat recovery and recycling of waste hot steel slag empty ladle from continuous casting and rolling (CSP). see figure 1 , the process is carried out in turn as follows:
[0026] a. Pour the excess heat slag into the empty ladle: After the CSP pouring is completed, hoist the steel ladle 8 filled with the excess heat slag to the ladle crossing car 10 with a crane, and then drive the crossing car 10 to the ladle to prepare for crossing , and then hoist the steel ladle 8 to the empty steel ladle 3 that is about to be tapped with a crane, and pour the residual hot steel slag poured from CSP in the steel ladle 8 into the empty steel ladle 3; Realize converter tapping.
[0027] b. Tapping: drive the ladle car carrying the ladle 3 of poured waste heat slag to converter 1, and tap the ladle filled with poured waste heat slag; at the beginning of tapping, the amount of bottom blowing argon is relatively large, and then the bottom blowing is reduc...
PUM
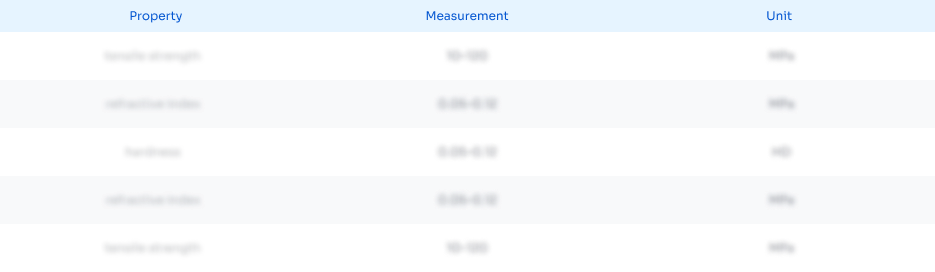
Abstract
Description
Claims
Application Information

- R&D
- Intellectual Property
- Life Sciences
- Materials
- Tech Scout
- Unparalleled Data Quality
- Higher Quality Content
- 60% Fewer Hallucinations
Browse by: Latest US Patents, China's latest patents, Technical Efficacy Thesaurus, Application Domain, Technology Topic, Popular Technical Reports.
© 2025 PatSnap. All rights reserved.Legal|Privacy policy|Modern Slavery Act Transparency Statement|Sitemap|About US| Contact US: help@patsnap.com