Metal glass melt cast moulding method and its device
A metal glass, casting and forming technology, applied in the field of metallurgy and metal material processing, can solve the problems of high equipment requirements, easy generation of pores in the sample, large equipment investment, etc. Effect
- Summary
- Abstract
- Description
- Claims
- Application Information
AI Technical Summary
Problems solved by technology
Method used
Image
Examples
example 1
[0039] Melting magnesium-based metallic glass material in a resistance furnace, the composition is Mg 65 Cu 25 Y 10 . It is melted under the protection of Ar gas, and the pouring temperature of the metallic glass melt is controlled between 580 and 700°C through PID adjustment. The sample diameter of the copper mold is 3mm. Utilize the negative pressure suction casting forming method to form, first pass through the control valve 6, the pressure measuring device 7 and the negative pressure stabilizing device 8, the negative pressure degree (vacuum degree) of the negative pressure generator 5 control device is 8kPa. Connect the mold with the suction pipe at the lower end and the pipeline connection device at the upper end. When pouring, insert the suction tube into the metal melt, open the control valve, and the metal glass melt in the crucible will rise into the cavity of the copper mold through the suction tube under the action of negative pressure. When the mold is full, ...
example 2
[0041] Melting aluminum-based metallic glass material with composition Al in a resistance furnace 85 Ni 5 Y 8 co 2 . It is melted under the protection of Ar gas, and the pouring temperature of the metallic glass melt is controlled between 700 and 750°C through PID adjustment. The parts of the copper mold are plate-shaped parts with an average thickness of 2mm. Utilize the negative pressure suction pouring forming method to form, first pass through the control valve 6, the pressure measuring device 7 and the negative pressure stabilizing device 8, the negative pressure degree (vacuum degree) of the negative pressure generator 5 control device is 10kPa. When pouring, insert the suction tube into the metal melt, open the control valve, and the metal glass melt in the crucible will rise into the cavity of the copper mold through the suction tube under the action of negative pressure. When the mold is full, close the control valve, lift the copper mold and the suction tube out...
example 3
[0043] Melting magnesium-based metallic glass material in a resistance furnace, the composition is Mg 75 Ni 15 Nd 10 . It is melted under the protection of Ar gas, and the pouring temperature of the metallic glass melt is controlled between 650 and 750°C through PID adjustment. The part cavity of the copper mold is a thin plate with an average wall thickness of 2mm. Utilize negative pressure-differential pressure forming method to form, first pass through control valve 6, pressure measuring device 7 and negative pressure stabilizing device 8, the negative pressure degree (vacuum degree) of negative pressure generator 5 control device is 5kPa. Connect the mold with the suction pipe at the lower end and the connection pipe at the upper end. When pouring, insert the suction pipe into the metal melt, and use the protective gas device and the flow pressure controller to control the gas pressure of the liquid surface of the metal glass melt in the crucible to 10kPa. Open the co...
PUM
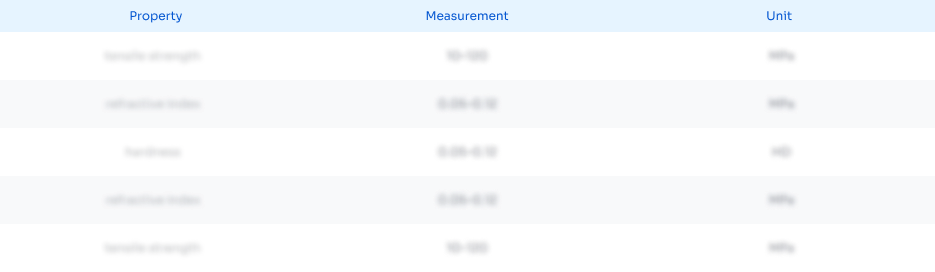
Abstract
Description
Claims
Application Information

- R&D
- Intellectual Property
- Life Sciences
- Materials
- Tech Scout
- Unparalleled Data Quality
- Higher Quality Content
- 60% Fewer Hallucinations
Browse by: Latest US Patents, China's latest patents, Technical Efficacy Thesaurus, Application Domain, Technology Topic, Popular Technical Reports.
© 2025 PatSnap. All rights reserved.Legal|Privacy policy|Modern Slavery Act Transparency Statement|Sitemap|About US| Contact US: help@patsnap.com