Method and apparatus for real-time automatic correction of shield attitude deviation
An automatic deviation correction device and a technology of shield attitude, which are applied in the field of automatic deviation correction technology, can solve the problems of unsatisfactory test results, low precision, and large cumulative error, and are beneficial to on-site construction management, avoiding large axis fluctuations, and improving The effect of construction quality
- Summary
- Abstract
- Description
- Claims
- Application Information
AI Technical Summary
Problems solved by technology
Method used
Image
Examples
specific Embodiment approach
[0028] The specific embodiment: the present invention will be further described in conjunction with accompanying drawing now
[0029] The measuring robot Leica TCA 1800 (total station 2) with remote control and automatic function is installed in the built tunnel to automatically measure the three targets pre-installed in the shield machine 8—metal reflector 5 and metal reflector 6 and the spatial position of the metal reflector 7, according to the rigid body space solution theory and the vector solution algorithm, the attitude parameters of the shield are calculated by the program pre-programmed by the total station 2, and are wirelessly transmitted through the signal control box 1 of the total station and the radio station 13. Send to the industrial control computer 12, the cycle period of the total station 2 measuring the attitude parameters of the shield can be set according to the needs, wherein the metal reflector 5, the metal reflector 6 and the metal reflector 7 can be i...
PUM
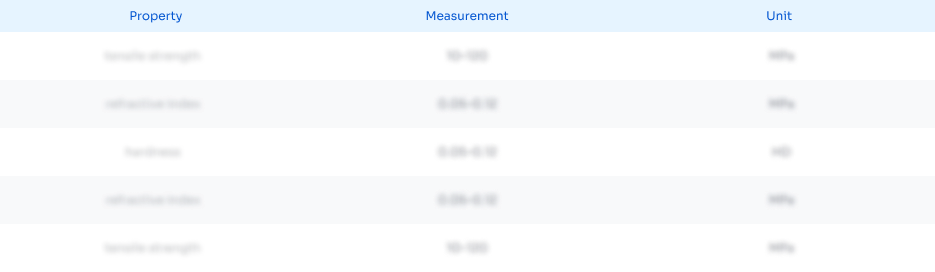
Abstract
Description
Claims
Application Information

- R&D
- Intellectual Property
- Life Sciences
- Materials
- Tech Scout
- Unparalleled Data Quality
- Higher Quality Content
- 60% Fewer Hallucinations
Browse by: Latest US Patents, China's latest patents, Technical Efficacy Thesaurus, Application Domain, Technology Topic, Popular Technical Reports.
© 2025 PatSnap. All rights reserved.Legal|Privacy policy|Modern Slavery Act Transparency Statement|Sitemap|About US| Contact US: help@patsnap.com