Plasma etching method of reducing generation of fine dust
A plasma etching, oxygen plasma technology, applied in the direction of electrical components, semiconductor/solid-state device manufacturing, circuits, etc., can solve problems such as affecting the conduction properties of the circuit 130, and achieve the effect of avoiding the generation of dust and defects
- Summary
- Abstract
- Description
- Claims
- Application Information
AI Technical Summary
Problems solved by technology
Method used
Image
Examples
Embodiment Construction
[0021] figure 2 What is shown is a schematic flow chart of a plasma etching method for reducing dust generation according to a preferred embodiment of the present invention. Please refer to figure 2 , The plasma etching method for reducing dust generation of the present invention at least includes an etching step 210 , a conversion step 220 , an etching step 230 and an oxygen plasma cleaning step 240 . Firstly, an etching step 210 is performed using an appropriate etching condition to etch the substrate. Then, before proceeding to the next etching step 230, a transition step 220 is performed. In this transition step 220, the plasma does not need to be turned off, so the temperature of the reaction chamber does not cool down. Then, after the etching step 230, an oxygen plasma cleaning step 240 is performed to remove plasma etching residues.
[0022] Such as figure 2 As shown, both the etching step 210 and the etching step 230 use plasma ionized gas to etch the substrate ...
PUM
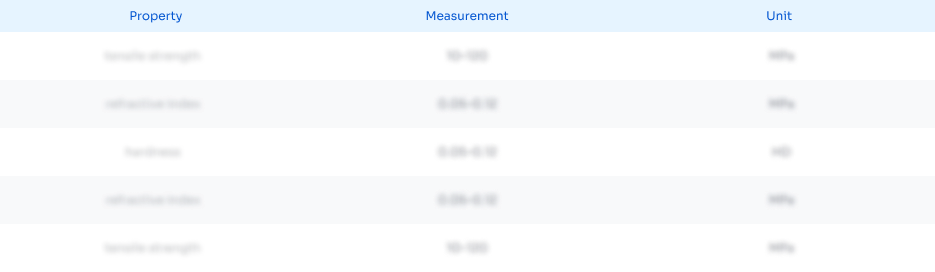
Abstract
Description
Claims
Application Information

- Generate Ideas
- Intellectual Property
- Life Sciences
- Materials
- Tech Scout
- Unparalleled Data Quality
- Higher Quality Content
- 60% Fewer Hallucinations
Browse by: Latest US Patents, China's latest patents, Technical Efficacy Thesaurus, Application Domain, Technology Topic, Popular Technical Reports.
© 2025 PatSnap. All rights reserved.Legal|Privacy policy|Modern Slavery Act Transparency Statement|Sitemap|About US| Contact US: help@patsnap.com