Technique and equipment for lowering formaldehyde in procedure for processing lumber-core board
A processing and blockboard technology, applied in wood processing utensils, impregnated wood, manufacturing tools, etc., can solve the problems of low free formaldehyde content, high free formaldehyde release, slow curing speed, etc., to reduce the content of free formaldehyde , The effect of reducing free formaldehyde content and reducing aging time
- Summary
- Abstract
- Description
- Claims
- Application Information
AI Technical Summary
Problems solved by technology
Method used
Image
Examples
Embodiment 1
[0021] Embodiment 1, the modulation formula of the urea-formaldehyde gluing used for wood strip splicing is (by weight): urea-formaldehyde resin 100, filler 20, formaldehyde trapping agent 6, curing agent 0.6; Form the core board, the poplar core board can be (by weight) urea-formaldehyde resin 100, filler 25, formaldehyde trapping agent 6, curing agent 0.4 to the requirement of gluing for the poplar core board; The board’s requirements for gluing are: (by weight): 100 urea-formaldehyde resin, 22 fillers, 6 formaldehyde scavenger, and 0.5 curing agent.
Embodiment 2
[0022] Embodiment 2, the formula of the urea-formaldehyde gluing used for splicing wood strips can be (parts by weight): urea-formaldehyde resin 100, filler 23, curing agent 0.8; poplar core board can be (parts by weight) low-formaldehyde urea-formaldehyde Resin 100, filler 28, curing agent 0.50; the requirements of the surface plate for gluing are: (by weight): urea-formaldehyde resin 100, filler 25, curing agent 0.50.
Embodiment 3
[0023] Embodiment 3, the formula of the urea-formaldehyde gluing used for wood strip splicing can be (by weight): low-formaldehyde urea-formaldehyde resin 100, filler 27, curing agent 0.9; Formaldehyde urea-formaldehyde resin 100, filler 33, curing agent 0.5; the surface plate is glued to the requirements: (by weight): low-formaldehyde urea-formaldehyde resin 100, filler 28, curing agent 0.5.
PUM
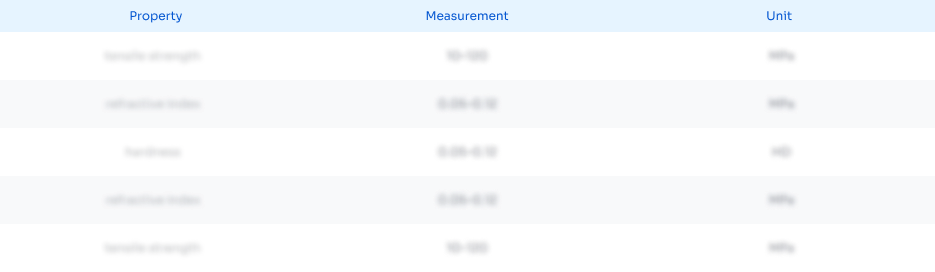
Abstract
Description
Claims
Application Information

- R&D
- Intellectual Property
- Life Sciences
- Materials
- Tech Scout
- Unparalleled Data Quality
- Higher Quality Content
- 60% Fewer Hallucinations
Browse by: Latest US Patents, China's latest patents, Technical Efficacy Thesaurus, Application Domain, Technology Topic, Popular Technical Reports.
© 2025 PatSnap. All rights reserved.Legal|Privacy policy|Modern Slavery Act Transparency Statement|Sitemap|About US| Contact US: help@patsnap.com