Method for processing spiral bevel gear and apparatus for forming large wheel of bevel gear thereof
A technology of spiral bevel gear and processing method, which is applied to components with teeth, belts/chains/gears, gear teeth, etc., which can solve problems such as difficult adjustments and affecting the processing accuracy of gears, and achieve high precision effects
- Summary
- Abstract
- Description
- Claims
- Application Information
AI Technical Summary
Problems solved by technology
Method used
Image
Examples
Embodiment Construction
[0012] A processing method for a spiral bevel gear, characterized in that: a half hobbing method is adopted, wherein the surface of both sides of the teeth of the small wheel is cut out by the generating method, the big wheel is cut out by the forming method, and the tooth profile of the concave and convex surface of the big wheel is processed Different shapes of cutterheads are used for forming respectively. First, the shape of each formed cutterhead is adjusted and modified according to the requirements of the contact area in the height direction, and then the modified cutterheads are installed on the respective cutterhead axes of the same machine tool. Each cutter head is adjusted by its own vertical guide rail, and its movement is controlled by a common transverse guide rail and feed guide rail, and different cutter heads are used to process the concave and convex surfaces of the large wheel.
[0013] Such as figure 1 , 2 As shown, a bevel gear wheel forming device includ...
PUM
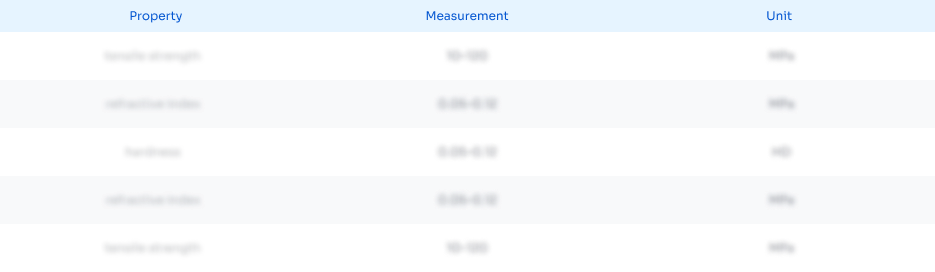
Abstract
Description
Claims
Application Information

- R&D Engineer
- R&D Manager
- IP Professional
- Industry Leading Data Capabilities
- Powerful AI technology
- Patent DNA Extraction
Browse by: Latest US Patents, China's latest patents, Technical Efficacy Thesaurus, Application Domain, Technology Topic, Popular Technical Reports.
© 2024 PatSnap. All rights reserved.Legal|Privacy policy|Modern Slavery Act Transparency Statement|Sitemap|About US| Contact US: help@patsnap.com