Method for preparing Fe-based WC-Ni gradient coating by using plasma cladding method
A technology of plasma cladding and gradient coating, applied in the direction of coating, metal material coating process, etc., can solve the problems of expensive equipment, easy coating falling off, hindering crack propagation, etc., to achieve strong shape and size adaptability and material selection range. Wide, mobile and flexible effects
- Summary
- Abstract
- Description
- Claims
- Application Information
AI Technical Summary
Problems solved by technology
Method used
Image
Examples
Embodiment Construction
[0023] The method for preparing five layers of WC-Ni reinforced Fe-based gradient coatings on the Q235 substrate will be described in detail below.
[0024] Among them, the specific composition (Wt%) of WC-Ni is 65%Ni60A+35WC%, and the specific composition (Wt%) of Fe-based powder is: C is (0.1%-0.3%), B is (1.2%-1.8%) , Si is (2.5%-3.5%), Cr is (4.0%-8.0%), Ni is (20%-35%), Fe is the balance, and the powder particle size is 150-300 mesh;
[0025] (1), add WC-Ni and Fe powder respectively in the A, B container of double barrel powder feeder ( figure 1 shown), the amount of powder fed is controlled by adjusting the speed of the scraper of the powder feeder. In this example, the proportions of the first to fifth layers of WC-Ni are 10%, 20%, 30%, 40%, and 50%, respectively, and the corresponding proportions of Fe are 90%, 80%, 70%, 60%, 50%. After the first layer is prepared, adjust the amount of powder feeding, and then prepare the second layer. The powder feeder is connect...
PUM
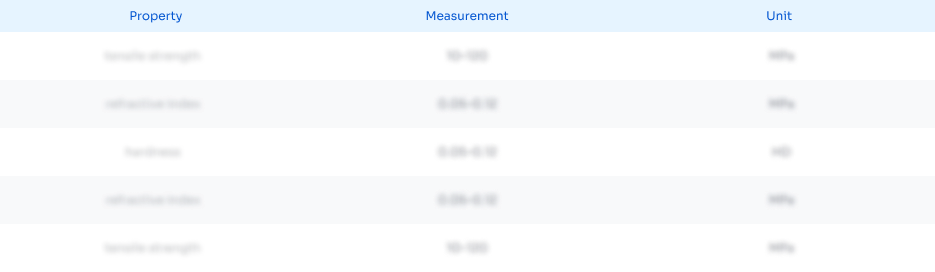
Abstract
Description
Claims
Application Information

- R&D
- Intellectual Property
- Life Sciences
- Materials
- Tech Scout
- Unparalleled Data Quality
- Higher Quality Content
- 60% Fewer Hallucinations
Browse by: Latest US Patents, China's latest patents, Technical Efficacy Thesaurus, Application Domain, Technology Topic, Popular Technical Reports.
© 2025 PatSnap. All rights reserved.Legal|Privacy policy|Modern Slavery Act Transparency Statement|Sitemap|About US| Contact US: help@patsnap.com