Dynamic pressure bearing production method
A technology for dynamic pressure bearings and manufacturing methods, applied to bearing components, shafts and bearings, mechanical equipment, etc., can solve the problems of difficult sharp formation, insufficient hardness of axial dynamic pressure concave parts, difficult formation, etc., and achieve high deformation Effect
- Summary
- Abstract
- Description
- Claims
- Application Information
AI Technical Summary
Problems solved by technology
Method used
Image
Examples
Embodiment
[0056] Next, examples of the present invention will be described to clarify the effects of the present invention.
[0057] Using a mixed powder of copper powder: 49% by mass, iron powder: 49% by mass, and tin powder: 2% by mass as the raw material powder, compression molding was performed by changing the molding pressure, and the obtained green compact was sintered to produce 8 kinds of densities ranging from 6.5 to 7.6Mg / m 3 sintered bearing raw materials. For these sintered bearing raw materials, using the method described in the above-mentioned embodiment, excluding the one used for comparison, the hole sealing treatment was performed on one end surface by ultrasonic machining, and then, the shape was formed on the one end surface. figure 2 The same separation grooves and arcuate surfaces as shown were used to obtain dynamic pressure bearings with sample numbers 1 to 8 shown in Table 1. In this case, sample No. 5 is a sample not subjected to ultrasonic processing.
[00...
PUM
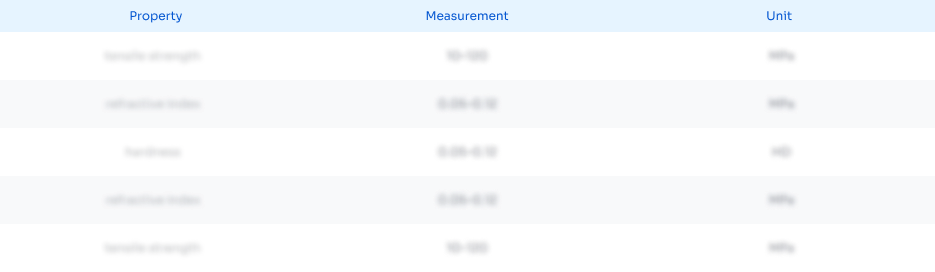
Abstract
Description
Claims
Application Information

- R&D
- Intellectual Property
- Life Sciences
- Materials
- Tech Scout
- Unparalleled Data Quality
- Higher Quality Content
- 60% Fewer Hallucinations
Browse by: Latest US Patents, China's latest patents, Technical Efficacy Thesaurus, Application Domain, Technology Topic, Popular Technical Reports.
© 2025 PatSnap. All rights reserved.Legal|Privacy policy|Modern Slavery Act Transparency Statement|Sitemap|About US| Contact US: help@patsnap.com