Complexing agent for preparing tungsten carbide granule reinforced steel matrix skin layer composite material
A technology of tungsten carbide particles and composite materials, applied in the field of materials, can solve the problems of difficult to manufacture parts, long production cycle, increased manufacturing cost, etc., and achieve the effect of improving structure and performance, less bad residues, and moderate bonding strength
- Summary
- Abstract
- Description
- Claims
- Application Information
AI Technical Summary
Problems solved by technology
Method used
Examples
Embodiment 1
[0009] The backbone material is 16% of thermosetting water-soluble phenolic resin, 8% of borax, 2% of 300-mesh aluminum powder, 2% of 270-mesh high-carbon ferrochrome powder, 1% of 270-mesh ferromolybdenum powder, and the rest is water. The backbone material is dissolved in water to make a solution, and the auxiliary materials are dispersed in the solution to make a composite agent. Fully stir the prepared composite agent to make it uniform, then add it into the tungsten carbide particles, continue to stir, so that the composite agent is evenly coated on the tungsten carbide particles, remove the water by heating, and then cast. The compounding agent is used to prepare WCp reinforced steel base surface layer composite rolling guide plate, the surface of the cast guide plate is smooth and smooth, the composite structure and the matrix structure are well combined, and the comprehensive performance of the composite material is very good.
Embodiment 2
[0011] The difference between this embodiment and Example 1 is that the backbone material is 20% of thermosetting water-soluble phenolic resin, 10% of borax, and the auxiliary material is 3% of 300 mesh aluminum powder, 2% of 270 mesh high carbon ferrochrome powder, 270 mesh Mesh molybdenum iron powder 2%, the rest is water. The backbone material is dissolved in water to make a solution, and the auxiliary materials are dispersed in the solution to make a composite agent. All the other are the same as in Example 1.
Embodiment 3
[0013] The difference between this embodiment and Example 1 is that the backbone material is 10% of thermosetting water-soluble phenolic resin, 5% of borax, and the auxiliary material is 3% of 300 mesh aluminum powder, 3% of 270 mesh high carbon ferrochrome powder, 270 mesh Mesh ferromolybdenum powder 1%, the rest is water. The backbone material is dissolved in water to make a solution, and the auxiliary materials are dispersed in the solution to make a composite agent. All the other are the same as in Example 1.
PUM
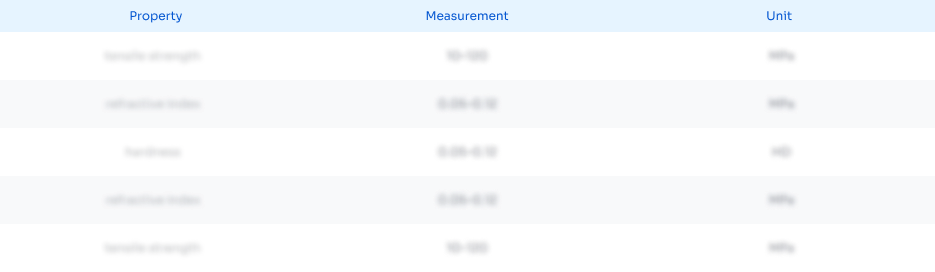
Abstract
Description
Claims
Application Information

- Generate Ideas
- Intellectual Property
- Life Sciences
- Materials
- Tech Scout
- Unparalleled Data Quality
- Higher Quality Content
- 60% Fewer Hallucinations
Browse by: Latest US Patents, China's latest patents, Technical Efficacy Thesaurus, Application Domain, Technology Topic, Popular Technical Reports.
© 2025 PatSnap. All rights reserved.Legal|Privacy policy|Modern Slavery Act Transparency Statement|Sitemap|About US| Contact US: help@patsnap.com