Method for mfg. plasma display
A plasma and manufacturing method technology, applied in the direction of discharge tube/lamp manufacturing, cold cathode manufacturing, tube/lamp screen manufacturing, etc., can solve problems such as poor crimping effect, broken glass substrate, and infirmity, etc., to achieve Improve crimping efficiency and success rate, prevent damage, and achieve uniform bonding
- Summary
- Abstract
- Description
- Claims
- Application Information
AI Technical Summary
Problems solved by technology
Method used
Examples
Embodiment 1
[0015] First, paste the anisotropic conductive film ACF film on the printed electrode of the glass substrate; then, put the glass substrate with the anisotropic conductive film ACF film on the crimping machine for low-temperature pre-compression, and heat the glass substrate up and down at the same time. 100℃, the pressure is 5Kg / cm 2 ; Secondly, peel off the upper layer of the anisotropic conductive film ACF film, leaving the adhesive layer of the anisotropic conductive film ACF film; paste the flexible circuit board film FPC film on the printed electrode of the glass substrate and paste the anisotropic conductive film ACF film, and then The glass substrate is heated up and down at the same time, the temperature is 80℃, and the pressure is 4~6Kg / cm 2 ; When the plasma glass substrate is heated, a rubber elastic soft gasket is placed on the heated glass substrate. Place the FPC film on the flexible circuit board on the crimping machine and press it firmly at a temperature of 200°C...
Embodiment 2
[0018] First, paste the anisotropic conductive film ACF film on the printed electrode of the glass substrate; then, put the glass substrate with the anisotropic conductive film ACF film on the crimping machine for low-temperature pre-compression, and heat the glass substrate up and down at the same time. 80℃, the pressure is 6Kg / cm 2 ; Secondly, peel off the upper layer of the anisotropic conductive film ACF film, leaving the adhesive layer of the anisotropic conductive film ACF film; paste the flexible circuit board film FPC film on the printed electrode of the glass substrate and paste the anisotropic conductive film ACF film, and then The glass substrate is heated up and down at the same time, the temperature is 100℃, and the pressure is 4~6Kg / cm 2 ; When the plasma glass substrate is heated, a rubber elastic soft gasket is placed on the heated glass substrate. Place the FPC film on the flexible circuit board on the crimping machine and press it firmly at a temperature of 180°C...
Embodiment 3
[0020] First, paste the anisotropic conductive film ACF film on the printed electrode of the glass substrate; then, put the glass substrate with the anisotropic conductive film ACF film on the crimping machine for low-temperature pre-compression, and heat the glass substrate up and down at the same time. 110℃, the pressure is 4Kg / cm 2 ; Secondly, peel off the upper layer of the anisotropic conductive film ACF film, leaving the adhesive layer of the anisotropic conductive film ACF film; paste the flexible circuit board film FPC film on the printed electrode of the glass substrate and paste the anisotropic conductive film ACF film, and then The glass substrate is heated up and down at the same time, the temperature is 110℃, and the pressure is 4~6Kg / cm 2 ; When the plasma glass substrate is heated, a plastic elastic soft gasket is placed on the heated glass substrate. Place the FPC film on the flexible circuit board on the crimping machine and press it firmly at a temperature of 210...
PUM
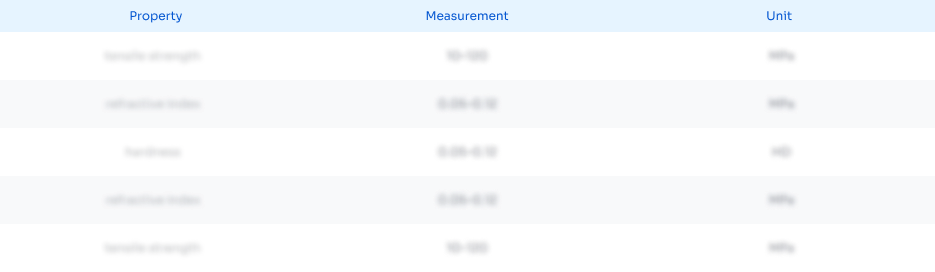
Abstract
Description
Claims
Application Information

- Generate Ideas
- Intellectual Property
- Life Sciences
- Materials
- Tech Scout
- Unparalleled Data Quality
- Higher Quality Content
- 60% Fewer Hallucinations
Browse by: Latest US Patents, China's latest patents, Technical Efficacy Thesaurus, Application Domain, Technology Topic, Popular Technical Reports.
© 2025 PatSnap. All rights reserved.Legal|Privacy policy|Modern Slavery Act Transparency Statement|Sitemap|About US| Contact US: help@patsnap.com