Technological process for surface low temperature boriding of low carbon steel
A process method, low carbon steel technology, applied in the direction of metal material coating process, coating, solid diffusion coating, etc., can solve the problems of high brittleness, high energy consumption, easy peeling of borides, and reduce the boronizing temperature. , Improve the boronizing efficiency and overcome the effect of large deformation
- Summary
- Abstract
- Description
- Claims
- Application Information
AI Technical Summary
Problems solved by technology
Method used
Examples
Embodiment 1
[0017] The low-temperature boronizing process steps of the present embodiment are as follows:
[0018] 1. Before boronizing, the surface of the low-carbon steel sample is nano-treated with a surface grinder.
[0019] In this embodiment, the existing SNC-1 metal surface nanometerization testing machine is adopted. This machine is equipped with a cooling water circulation device. A container is arranged in the machine, and a piece of low-carbon metal surface prepared for nanometerization treatment is fixed on the container cover. steel sample; small steel balls for nano shot blasting are housed in the container, and the diameter of the small steel balls is 8mm, 200 in total; the container cover is closed and sealed, and vacuumized; then the motor is started to drive the testing machine to rotate at a high speed, and A vibration generator is used to make the nano-sized shot-peening small steel balls move vigorously to perform nano-processing on the metal surface itself, and the p...
PUM
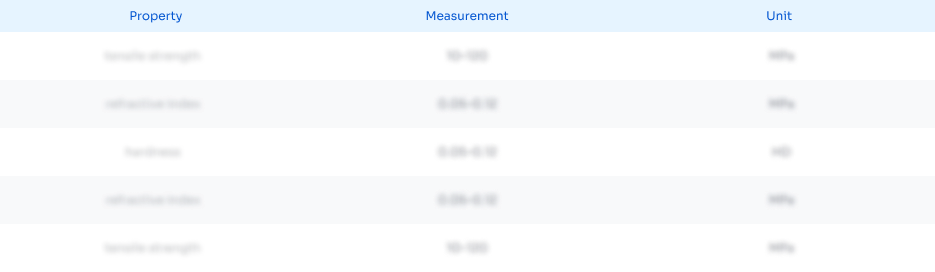
Abstract
Description
Claims
Application Information

- R&D
- Intellectual Property
- Life Sciences
- Materials
- Tech Scout
- Unparalleled Data Quality
- Higher Quality Content
- 60% Fewer Hallucinations
Browse by: Latest US Patents, China's latest patents, Technical Efficacy Thesaurus, Application Domain, Technology Topic, Popular Technical Reports.
© 2025 PatSnap. All rights reserved.Legal|Privacy policy|Modern Slavery Act Transparency Statement|Sitemap|About US| Contact US: help@patsnap.com