Method for preparing acrylic ester and separation 1, 2-dichloropropane by using DD mixing agent
A technology of dichloropropane and acrylate, which is applied in the field of comprehensive utilization of chemical by-products - DD mixture, which can solve problems such as imperfect treatment methods and difficult rectification separation
- Summary
- Abstract
- Description
- Claims
- Application Information
AI Technical Summary
Problems solved by technology
Method used
Image
Examples
Embodiment 1
[0041] Embodiment 1 (two-step method)
[0042] The DD mixture was dehydrated and simply distilled to remove impurities, and its component content was analyzed by gas chromatography. The acrylic acid is refined by vacuum distillation to remove possible polymers and impurities, and an appropriate amount of polymerization inhibitor is added to prevent its polymerization.
[0043] After installing a stirring device, a water separator, and a condenser on the there-necked flask, add 36 g (0.5 mol) of acrylic acid and 0.04 g of a polymerization inhibitor DPPH, stir and cool, and add 20 g (0.5 mol) of sodium hydroxide to neutralize. Then use benzene azeotropic dehydration, vacuum drying to obtain about 47g of sodium acrylate.
[0044] After installing stirring device, condenser and thermometer on the 500ml there-necked flask, add DD mixture 241.3g (containing 1,3-dichloropropene 23%, 0.5mol), sodium acrylate 47g (0.5mol), DPPH0. 04g, triethylamine 3ml. Heat the oil bath to 85-90°C,...
Embodiment 2
[0045] Embodiment 2 (two-step method)
[0046] Implementation steps are the same as in Example 1. The conditions of the esterification reaction were changed as follows: the reaction temperature was 75-80° C., the reaction time was 4 hours, and the amount of triethylamine was 2.5 ml, so the yield of 3-chloro-2-propenyl acrylate was 6.8%.
Embodiment 3
[0047] Embodiment 3 (two-step method)
[0048] Implementation steps are the same as in Example 1. The conditions of the esterification reaction were changed to: the reaction temperature was 75-80°C, the reaction time was 5 hours, and the amount of triethylamine was 3.0ml, so the yield of 3-chloro-2-propenyl acrylate was 22.7%.
PUM
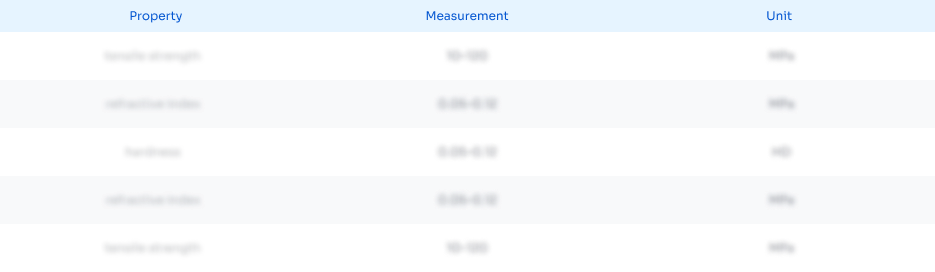
Abstract
Description
Claims
Application Information

- Generate Ideas
- Intellectual Property
- Life Sciences
- Materials
- Tech Scout
- Unparalleled Data Quality
- Higher Quality Content
- 60% Fewer Hallucinations
Browse by: Latest US Patents, China's latest patents, Technical Efficacy Thesaurus, Application Domain, Technology Topic, Popular Technical Reports.
© 2025 PatSnap. All rights reserved.Legal|Privacy policy|Modern Slavery Act Transparency Statement|Sitemap|About US| Contact US: help@patsnap.com