Method for producing 1, 3-dimethyl -2-imidazolinone
An imidazolinone and production method technology, applied in the field of synthesis 1, can solve the problems of low product purity, low product yield, high raw material cost, etc., and achieve the effects of wide sources, high conversion rate, and less three wastes
- Summary
- Abstract
- Description
- Claims
- Application Information
AI Technical Summary
Problems solved by technology
Method used
Image
Examples
Embodiment 1
[0019] Add 305Kg of ethylenediamine, 391Kg of urea, and 549Kg of water into a 3000-liter reactor, stir and dissolve, react at 100-160°C for 15 hours, cool, crystallize, filter, and wash the filter cake with water three times to obtain 2- The imidazolinone crude product is 432Kg.
[0020] Add 344Kg of 2-imidazolinone, 1800Kg of 80% formic acid, and 1300Kg of 36% formaldehyde in a 5000-liter reactor, stir and dissolve, and react at 120°C for 16 hours, steam the unreacted formaldehyde, Formic acid and water, add cuprous chloride 50Kg, triethylamine 13Kg, stir and react at 120°C for 6 hours; cool to room temperature, filter, take the filtrate, distill, collect the fraction above 100°C, add anhydrous calcium chloride , stirred, and filtered; 375Kg of 1,3-dimethyl-2-imidazolidinone was obtained. After analysis, the product content was 99.51%, and the moisture content was 0.10%.
Embodiment 2
[0022] Add 305Kg of ethylenediamine, 391Kg of urea, and 275Kg of water into a 3,000-liter reactor, stir and dissolve, react at 100-160°C for 15 hours, cool, crystallize, filter, and wash the filter cake with water three times to obtain 2- The imidazolinone crude product is 512Kg.
[0023] Add 344Kg of 2-imidazolinone, 1800Kg of 80% formic acid, and 1300Kg of 36% formaldehyde in a 5000-liter reactor, stir and dissolve, and react at 120°C for 16 hours, steam the unreacted formaldehyde, Formic acid and water, add cuprous chloride 50Kg, triethylamine 13Kg, stir and react at 120°C for 6 hours; cool to room temperature, filter, take the filtrate, distill, collect the fraction above 100°C, add anhydrous calcium chloride , stirred, and filtered; 295Kg of 1,3-dimethyl-2-imidazolidinone was obtained. After analysis, the product content was 97.58%, and the moisture content was 0.18%.
Embodiment 3
[0025] Add 305Kg of ethylenediamine, 391Kg of urea, and 840Kg of water into a 3000-liter reactor, stir and dissolve, react at 100-160°C for 15 hours, cool, crystallize, filter, and wash the filter cake with water three times to obtain 2- The imidazolinone crude product is 372Kg.
[0026] Add 344Kg of 2-imidazolinone, 1800Kg of 80% formic acid, and 1300Kg of 36% formaldehyde in a 5000-liter reactor, stir and dissolve, and react at 120°C for 16 hours, steam the unreacted formaldehyde, Formic acid and water, add cuprous chloride 50Kg, triethylamine 13Kg, stir and react at 120°C for 6 hours; cool to room temperature, filter, take the filtrate, distill, collect the fraction above 100°C, add anhydrous calcium chloride , stirred, and filtered; 370Kg of 1,3-dimethyl-2-imidazolidinone was obtained. After analysis, the product content was 99.48%, and the moisture content was 0.12%.
PUM
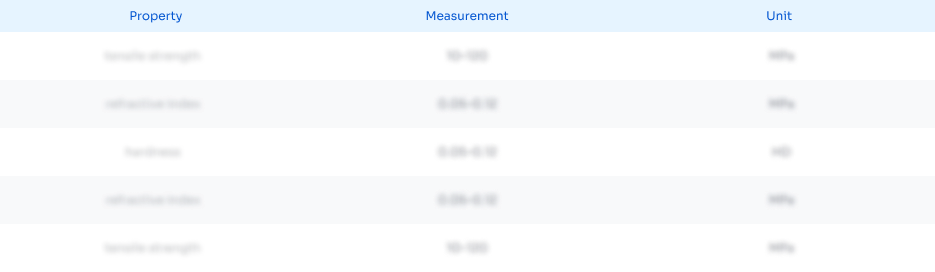
Abstract
Description
Claims
Application Information

- R&D
- Intellectual Property
- Life Sciences
- Materials
- Tech Scout
- Unparalleled Data Quality
- Higher Quality Content
- 60% Fewer Hallucinations
Browse by: Latest US Patents, China's latest patents, Technical Efficacy Thesaurus, Application Domain, Technology Topic, Popular Technical Reports.
© 2025 PatSnap. All rights reserved.Legal|Privacy policy|Modern Slavery Act Transparency Statement|Sitemap|About US| Contact US: help@patsnap.com