Sintering formula and process for sand wheel
A technology of grinding wheel and formula, which is applied in the direction of manufacturing tools, metal processing equipment, abrasives, etc., can solve the problems of insufficient grinding wheel, sand, thallium, black seven, and roughness, etc., and achieve the effect of reducing scratches, good effect, and avoiding burns
- Summary
- Abstract
- Description
- Claims
- Application Information
AI Technical Summary
Problems solved by technology
Method used
Examples
specific Embodiment
[0016] 1. Shoulder material: green silicon carbide 70~90% microcrystalline corundum 10-30% (by weight),
[0017] 2. Binder: clay 15-35%, feldspar 50-70%, boron glass 10-15% (by weight);
[0018] 3. Grinding wheel hardness: R3-ZR1,
[0019] 4. Organization number: No. 6~7:
[0020] 5. Sintering process, using city gas, using a 36-meter tunnel kiln, the firing temperature is 1330-1350 ° C, and the firing time is 90-100 hours. The grinding wheel and the corundum grinding wheel are clamped to oxidize the filling atmosphere or neutral Burning in a flame atmosphere can avoid black hearts and burning bubbles.
PUM
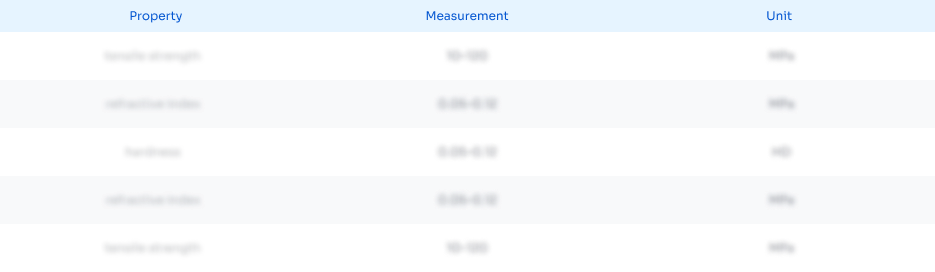
Abstract
Description
Claims
Application Information

- R&D Engineer
- R&D Manager
- IP Professional
- Industry Leading Data Capabilities
- Powerful AI technology
- Patent DNA Extraction
Browse by: Latest US Patents, China's latest patents, Technical Efficacy Thesaurus, Application Domain, Technology Topic, Popular Technical Reports.
© 2024 PatSnap. All rights reserved.Legal|Privacy policy|Modern Slavery Act Transparency Statement|Sitemap|About US| Contact US: help@patsnap.com