Preparation for continuous fibre reinforced poly(phthalazinone ehter sulfone ketone) composite materials
An advanced composite material, polyarylethersulfone ketone technology, applied in the field of advanced composite materials science
- Summary
- Abstract
- Description
- Claims
- Application Information
AI Technical Summary
Problems solved by technology
Method used
Image
Examples
Embodiment 1
[0021] Dissolving polyarylether sulfone ketone (PPESK) in N, N-dimethylacetamide (DMAc) solvent, preparing a 20% (mass content) PPESK solution, impregnated continuous glass fibers, and prepared a prepreg sheet. The continuous glass fiber reinforced PPESK unidirectional composite material is prepared according to the following process:
[0022] Continuous fiber→prepreg→drying→fiber prepreg sheet
[0023] →Hot compression forming→Demoulding→Unidirectional plate→Test piece
[0024] The impregnation process for making fiber prepreg is shown in the table below.
[0025] Solution concentration Dipping temperature Traction speed Squeegee bar spacing Drying temperature Drying
[0026] time
[0027] 20~40% Room temperature 1.0m / min 1.5mm 170~200℃ for about 2min
[0028] In the preparation process of the invention, the prepreg sheet is prepared by fiber winding or pultrusion molding process, and then hot-pressed. The mai...
Embodiment 2
[0031] Dissolving polyarylether sulfone ketone (PPESK) in N, N-dimethylacetamide (DMAc) solvent, preparing a 20% (mass content) PPESK solution, and impregnating continuous carbon fibers to prepare a prepreg sheet. Continuous carbon fiber reinforced PPESK unidirectional composites were prepared according to the following process:
[0032] Continuous fiber→prepreg→drying→fiber prepreg sheet
[0033] →Hot compression forming→Demoulding→Unidirectional plate→Test piece
[0034] The impregnation process for making fiber prepreg is shown in the table below.
[0035] Solution concentration Dipping temperature Traction speed Squeegee bar spacing Drying temperature Drying time
[0036] 20~40% Room temperature 1.0m / min 1.5mm 170~200℃ for about 2min
[0037] In the preparation process of the invention, the prepreg sheet is prepared by fiber winding or pultrusion molding process, and then hot-pressed. The main process parameters of the thermoforming process are as follows:
[0038] Co...
Embodiment 3
[0040] Dissolving polyarylether sulfone ketone (PPESK) in N, N-dimethylacetamide (DMAc) solvent, preparing a 20% (mass content) PPESK solution, impregnated continuous aramid fiber, and prepared a prepreg sheet. The continuous aramid fiber reinforced PPESK unidirectional composite material was prepared according to the following process:
[0041] Continuous fiber→prepreg→drying→fiber prepreg sheet
[0042] →Hot compression forming→Demoulding→Unidirectional plate→Test piece
[0043] The impregnation process for making fiber prepreg is shown in the table below.
[0044] Solution concentration Dipping temperature Traction speed Squeegee bar spacing Drying temperature Drying time
[0045] 20~40% Room temperature 1.0m / min 1.5mm 170~200℃ for about 2min
[0046] In the preparation process of the invention, the prepreg sheet is prepared by fiber winding or pultrusion molding process, and then hot-pressed. The main process parameters of the thermoforming process are as follows:
[...
PUM
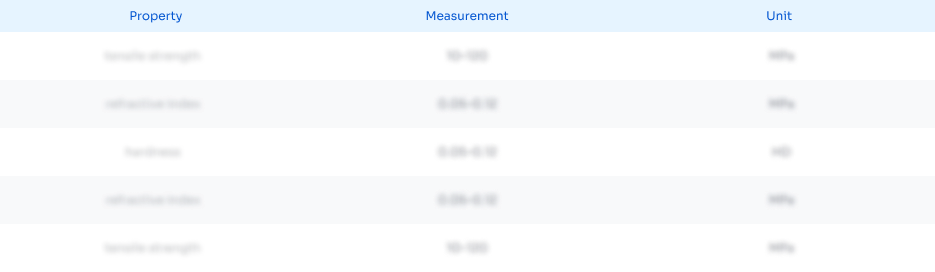
Abstract
Description
Claims
Application Information

- R&D
- Intellectual Property
- Life Sciences
- Materials
- Tech Scout
- Unparalleled Data Quality
- Higher Quality Content
- 60% Fewer Hallucinations
Browse by: Latest US Patents, China's latest patents, Technical Efficacy Thesaurus, Application Domain, Technology Topic, Popular Technical Reports.
© 2025 PatSnap. All rights reserved.Legal|Privacy policy|Modern Slavery Act Transparency Statement|Sitemap|About US| Contact US: help@patsnap.com