Mineral dressing method for black and white tungsten minerals
A beneficiation method, black and white tungsten technology, applied in flotation, solid separation, etc., can solve the problem of low grade of black and white tungsten mixed coarse concentrate, large amount of collector CF and activator, low yield of black and white tungsten mixed rough concentrate To achieve the effect of improving the comprehensive utilization rate of mine resources, high grade of tungsten coarse concentrate and high tungsten recovery rate
- Summary
- Abstract
- Description
- Claims
- Application Information
AI Technical Summary
Problems solved by technology
Method used
Image
Examples
Embodiment Construction
[0011] Crush the raw ore and grind it to -0.074mm, accounting for 80-85%. After removing the magnetite by magnetic separation and flotation to remove sulfide minerals, add water glass, aluminum sulfate, lead nitrate, and stir for 1-10 minutes; add and collect Benzohydroxamic acid, sulfated oleic acid soap or Tal soap and kerosene, stirred for 1-10 minutes; mixed flotation of black and white tungsten in neutral pulp medium, after 1 roughing, 2-5 times of concentration , 2-3 times of sweeping, the pH value of the tungsten flotation pulp is 6.5-8.5, and the concentration of the roughing pulp is 35-50%.
[0012] The floating sulfide tailings of Examples 1-4 contain WO 3 0.53%-0.55%, CaF 2 16-25%, of which the ratio of black and white tungsten is about 2.5:7.5.
[0013] The floating sulfide tailings of Examples 5-8 contain WO 3 0.63%-0.65%, CaF 2 16-25%, of which the ratio of black and white tungsten is about 4.0:6.0.
[0014] The floating sulfide tailings of Examples 9-10...
PUM
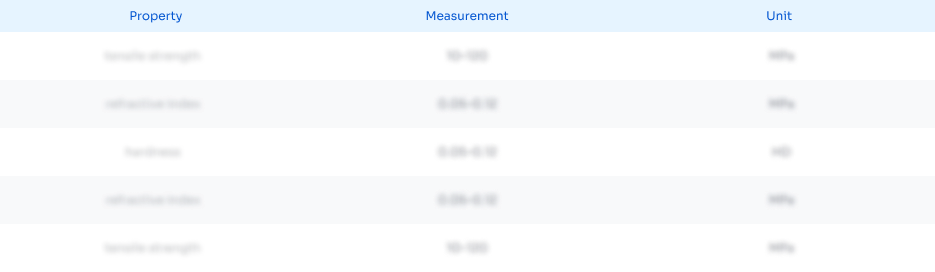
Abstract
Description
Claims
Application Information

- Generate Ideas
- Intellectual Property
- Life Sciences
- Materials
- Tech Scout
- Unparalleled Data Quality
- Higher Quality Content
- 60% Fewer Hallucinations
Browse by: Latest US Patents, China's latest patents, Technical Efficacy Thesaurus, Application Domain, Technology Topic, Popular Technical Reports.
© 2025 PatSnap. All rights reserved.Legal|Privacy policy|Modern Slavery Act Transparency Statement|Sitemap|About US| Contact US: help@patsnap.com