Thermostable strong acid cation resin catalyst and its preparing method
A strong acid cation, high temperature resistant technology, used in chemical instruments and methods, physical/chemical process catalysts, organic compound/hydride/coordination complex catalysts, etc. and other problems, to achieve the effect of improving uniformity, improving high-temperature mechanical stability, and reducing costs
- Summary
- Abstract
- Description
- Claims
- Application Information
AI Technical Summary
Problems solved by technology
Method used
Examples
Embodiment 1
[0049] (1) Polymerization: Add 20 liters of pure water into a 50-liter polymerization kettle, heat to 45°C, add 10 g of magnesium carbonate, 20 g of gelatin and 0.15 g of methine blue under stirring, and add 3 kg of benzene Ethylene, 1kg divinylbenzene, 20g benzoyl peroxide, 1kg white oil and 400g toluene mixed oil phase. Close the reaction kettle, feed clean compressed air into the reaction kettle, keep the gas phase pressure in the kettle at 0.5±0.05MPa, start stirring, adjust the liquid beads to an appropriate particle size, raise the temperature to 80°C, keep warm for 10 hours, filter, wash and dry , Screening to obtain 4.75 kg of white balls with a particle size of 0.315 to 1.120 mm.
[0050] (2) Solvent extraction: the white ball obtained in step (1) was extracted 5 times with 120# gasoline, after removing the porogen, dried to obtain 3.09 kg of semi-finished white ball.
[0051](3) Dichloroethane cooking: Add 3.09 kg of the above-mentioned white balls into a 50-liter r...
Embodiment 2
[0058] (1) Polymerization: Add 20 liters of pure water into a 50-liter polymerization kettle, heat to 45°C, add 10 g of magnesium carbonate, 20 g of gelatin and 0.15 g of methine blue under stirring, and add 3 kg of benzene Ethylene, 1kg divinylbenzene, 20g benzoyl peroxide mixed oil phase. Close the reaction kettle, feed clean compressed air into the reaction kettle, keep the gas phase pressure in the kettle at 0.5±0.05MPa, start stirring, adjust the liquid beads to an appropriate particle size, raise the temperature to 80°C, keep warm for 10 hours, filter, wash and dry , Screening to obtain 3.8 kg of white balls with a particle size of 0.315 to 1.120 mm.
[0059] (2) Dichloroethane cooking: Add 3.8 kg of the above-mentioned white balls into a 50-liter reactor equipped with a reflux condenser, then add 15 liters of dichloroethane, raise the temperature to 90°C, and maintain the pressure in the kettle at 0.3MPa for 10 hours , cooled to 15°C.
[0060] (3) Chlorination: Add 25...
Embodiment 3
[0065] Except that the halogenation process is different, the polymerization, solvent extraction, dichloroethane cooking, sulfonation, and resin pretreatment are all the same as in Example 1.
[0066] The halogenating agent of embodiment 3 is bromine, and its technological process is: add 770g white ball after dichloroethane cooking in 10 liters of reactors, then add 4kg dichloroethane, 8g anhydrous aluminum trichloride, stir to dissolve , at a temperature of 15±3°C, slowly add 1.9kg of bromine dropwise, and keep warm at this temperature for 6 hours, extract dichloroethane, and wash with fresh dichloroethane three times, 4kg each time. The washing liquid can be recycled after treatment. The resulting styrene-divinylbenzene copolymer with brominated benzene rings was then subjected to sulfonation and pretreatment in the same manner as in Example 1 to obtain a high temperature resistant resin catalyst with brominated benzene rings.
[0067] The finished resin catalyst of embodi...
PUM
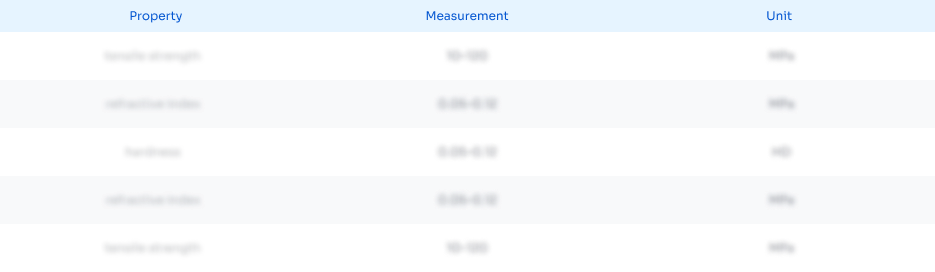
Abstract
Description
Claims
Application Information

- R&D
- Intellectual Property
- Life Sciences
- Materials
- Tech Scout
- Unparalleled Data Quality
- Higher Quality Content
- 60% Fewer Hallucinations
Browse by: Latest US Patents, China's latest patents, Technical Efficacy Thesaurus, Application Domain, Technology Topic, Popular Technical Reports.
© 2025 PatSnap. All rights reserved.Legal|Privacy policy|Modern Slavery Act Transparency Statement|Sitemap|About US| Contact US: help@patsnap.com