Multistage burning method and system for gasification of refuse and co-fusion of charcoal ash in rotary kiln
A technology of rotary kiln and garbage, applied in the direction of combustion method, incinerator, combustion type, etc., can solve the problem that the fly ash source cannot be effectively eliminated, does not involve any fly ash source, unfavorable metal resource recovery, etc., and achieves good adaptability and operability, reduce the cost of flue gas treatment, improve the effect of sealing effect
- Summary
- Abstract
- Description
- Claims
- Application Information
AI Technical Summary
Problems solved by technology
Method used
Image
Examples
Embodiment 1
[0032] Embodiment 1 (operation mode of gasification+melting combustion)
[0033]This embodiment realizes the gasification in the kiln body 1 of the rotary kiln gasification furnace (the air coefficient is 0.3 to 0.5, usually 0.4), and the gas, residual charcoal and fly ash are generated in the combustion chamber 19 of the downward high-temperature melting combustion furnace undergo melting combustion.
[0034] Such as figure 1 As shown, the steps are as follows: (1) the preliminary crushed garbage (particle size <20cm) enters the kiln body 1 through the hopper 2, the hydraulic valve 3, the piston feeder 4, and finally enters the kiln body 1 through the garbage inlet 5; Fuel is fed from the fuel nozzle 12 at the end of the kiln body 1, and the primary air is injected by the primary fan 15 through the primary tuyere 16. After starting, the fuel can be reduced or even shut down according to the temperature in the furnace; (3) garbage in the furnace and reverse high-temperature s...
Embodiment 2
[0035] Embodiment 2 (operation mode of initial combustion + high temperature melting type supplementary combustion)
[0036] What this embodiment achieves is combustion in the kiln body 1 of the rotary kiln gasification furnace (the air coefficient is 1.2), to generate flue gas and fly ash, and then enter the combustion chamber 19 of the downward-type high-temperature melting combustion furnace for supplementary combustion and melting.
[0037] The same part of this embodiment and the previous embodiment will not be described again, the difference lies in the step (5) described in Embodiment 1. Since this embodiment produces very little carbon residue during the combustion process, and it is mainly concentrated in fine carbon, it is only necessary to collect fine carbon below 1 mm, and there is no need for a crushing process of residual carbon. After collection, the fine carbon can be directly sent to high-temperature melting In the combustion chamber 19 of the combustion furn...
PUM
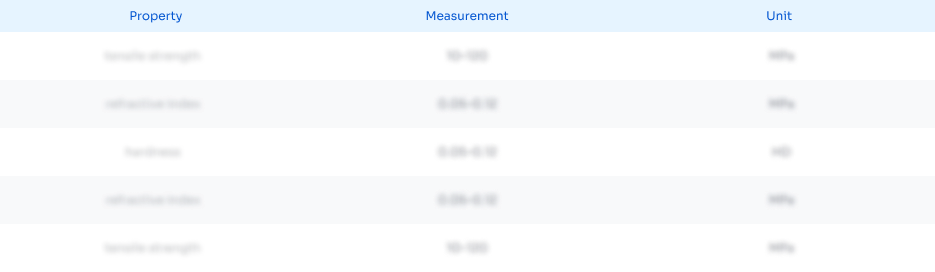
Abstract
Description
Claims
Application Information

- R&D
- Intellectual Property
- Life Sciences
- Materials
- Tech Scout
- Unparalleled Data Quality
- Higher Quality Content
- 60% Fewer Hallucinations
Browse by: Latest US Patents, China's latest patents, Technical Efficacy Thesaurus, Application Domain, Technology Topic, Popular Technical Reports.
© 2025 PatSnap. All rights reserved.Legal|Privacy policy|Modern Slavery Act Transparency Statement|Sitemap|About US| Contact US: help@patsnap.com