Catalytic cracking catalyst and preparing method thereof
A catalytic cracking and catalyst technology, used in catalytic cracking, cracking, petroleum industry and other directions, can solve the problem of the limited cracking capacity of cracking active catalyst macromolecules
- Summary
- Abstract
- Description
- Claims
- Application Information
AI Technical Summary
Problems solved by technology
Method used
Examples
example 1
[0039] Preparation of silica sol: prepare 2 liters of water glass solution and 1 liter of dilute acidified aluminum sulfate solution (free acid is 148g / l, aluminum oxide content is 20g / l) with 2 liters of silica concentration, and the above two solutions are simultaneously Enter into the rapid mixer reaction to obtain about 3 liters of silica sol.
[0040] Preparation of mixed slurry of kaolin, pseudo-boehmite and molecular sieve: take 300 grams of kaolin respectively, containing 15 grams of Al 2 o 3 Polyaluminum chloride, 175 grams of ground REUSY molecular sieve, 175 grams of ground PSRY molecular sieve, 200 grams of finely ground pseudo-boehmite containing alumina, mixed with deionized water for 2 hours, and then added 35 milliliters of hydrochloric acid (acid / Al 2 o 3 The weight ratio is 0.04) peptization, and the beating is continued for 30 minutes for later use, and the solid content of the mixed slurry is 42m%.
[0041] Preparation of catalyst: Mix 1.45 liters of the ...
example 2
[0043] Silica sol is prepared with example 1.
[0044] Preparation of mixed slurry of kaolin and pseudo-boehmite: take 300 grams of kaolin respectively, containing 8 grams of Al 2 o 3 Polyaluminum chloride, containing 200 grams of alumina finely ground pseudo-boehmite, mixed with deionized water for 2 hours, then added 35 milliliters of hydrochloric acid (acid / Al 2 o 3 The mass ratio is 0.04) peptization, and the beating is continued for 30 minutes for later use, and the solid content of the mixed slurry is 42m%.
[0045] Preparation of molecular sieve slurry: take 175 grams of ground REUSY molecular sieve and 175 grams of ground PSRY molecular sieve, and beat with deionized water.
[0046] Catalyst preparation: Mix 1.45 liters of silica sol, kaolin, pseudoboehmite mixed slurry and molecular sieve slurry prepared above in a rapidly stirring mixing tank to obtain a catalyst precursor slurry, which is then spray-dried and washed with ammonium sulfate aqueous solution , and d...
example 3
[0055] Catalyst F-1 of the present invention and contrast agent samples D-1 and D-2 were treated with 100% steam at 800°C for 4 hours, and then evaluated on a heavy oil micro-reactor device. Wax oil, reaction temperature 482°C, agent-oil ratio 3.5, space velocity 16.0h -1 , and the evaluation results are listed in Table 2.
[0056] As can be seen from Table 2, under the same reaction conditions, the catalyst F-1, D-1 conversion rate is higher than the catalyst D-2, indicating that the activity of the catalyst of the present invention is higher, when the pseudo-boehmite is completely peptized Catalyst D-2 is relatively poor in heavy oil conversion ability. In the product distribution, the heavy oil yield is 2 percentage points higher than that of catalyst sample F-1 of the present invention. The catalyst prepared by pseudoboehmite is not peptized and the reaction performance of catalyst sample of the present invention quite.
[0057] D-1
PUM
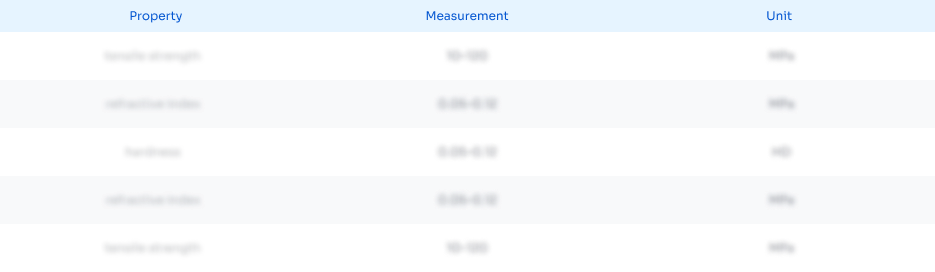
Abstract
Description
Claims
Application Information

- Generate Ideas
- Intellectual Property
- Life Sciences
- Materials
- Tech Scout
- Unparalleled Data Quality
- Higher Quality Content
- 60% Fewer Hallucinations
Browse by: Latest US Patents, China's latest patents, Technical Efficacy Thesaurus, Application Domain, Technology Topic, Popular Technical Reports.
© 2025 PatSnap. All rights reserved.Legal|Privacy policy|Modern Slavery Act Transparency Statement|Sitemap|About US| Contact US: help@patsnap.com