Aluminum silicon alloy series possessing granulated silicon phase and its process
A technology of an aluminum-silicon alloy and a process method, which is applied to the aluminum-silicon alloy series with a granular silicon phase and the process field thereof, can solve problems such as difficult popularization and application, difficult production process, etc., achieve high wear resistance, and avoid process difficulties. , light weight effect
- Summary
- Abstract
- Description
- Claims
- Application Information
AI Technical Summary
Problems solved by technology
Method used
Image
Examples
Embodiment 1
[0026]The chemical composition of the electrolytic eutectic aluminum-silicon alloy ingot is: Si 12.12%, Cu 0.88%, Mg 0.91%, Mn 0.01%, Ni 0.81%, Fe 0.25%, Ti 0.09%, Srfigure 1 ). After solution treatment at 500°C for 6 hours, the silicon phase transformed into particles, which were evenly distributed on the aluminum substrate, most of which were less than 5 μm in size. (See figure 2 ).
Embodiment 2
[0028] Electrolytic eutectic Al-Si alloy ingot. Chemical composition and melting process are the same as Example 1. Remelt 3 times. After solid solution treatment at 500°C for 6 hours, the silicon phase transforms into particles, which are evenly distributed on the aluminum substrate, with a slight increase in size, most of which are still less than 10 μm (see image 3 ). It shows that the spheroidization property of the silicon phase of the electrolytic Al-Si alloy gradually weakens with the increase of remelting times.
Embodiment 3
[0030] The chemical composition of the hypereutectic aluminum-silicon alloy is Si 13.7%, Cu 0.98%, Mg 0.55%, Mn 0.49%, Ni 0.30%, Fe 0.26%, Ti 0.08%, and Srfigure 1 Description), Al-25% Si master alloy. Melt in a resistance furnace. Raise the temperature to 720°C and degas with nitrogen. No modifiers are added. After 15 minutes of heat preservation, pour into the metal mold preheated to 300°C. The sample size is 45×50×120mm. In the as-cast metallographic structure of the alloy, no primary silicon phase appears, and the Al-Si eutectic and a large number of dendritic primary aluminum phases are the main components. The silicon phase is metamorphic, unusually fine and distorted. After solution treatment at 500°C for 6 hours, the silicon phase transformed into particles, which were evenly distributed on the aluminum substrate, most of which were less than 5 μm in size. Some larger silicon phases are distributed around the eutectic (see Figure 4 ). It shows that the addition...
PUM
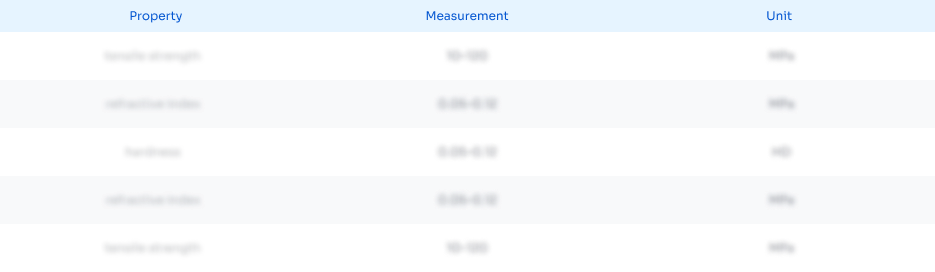
Abstract
Description
Claims
Application Information

- Generate Ideas
- Intellectual Property
- Life Sciences
- Materials
- Tech Scout
- Unparalleled Data Quality
- Higher Quality Content
- 60% Fewer Hallucinations
Browse by: Latest US Patents, China's latest patents, Technical Efficacy Thesaurus, Application Domain, Technology Topic, Popular Technical Reports.
© 2025 PatSnap. All rights reserved.Legal|Privacy policy|Modern Slavery Act Transparency Statement|Sitemap|About US| Contact US: help@patsnap.com