New technique for producing disodium phosphate
A new technology of sodium tripolyphosphate, applied in the direction of phosphorus compounds, inorganic chemistry, non-metallic elements, etc., can solve the problems of high cost and hidden danger of pollution, and achieve the effect of low cost and pollution reduction.
- Summary
- Abstract
- Description
- Claims
- Application Information
AI Technical Summary
Problems solved by technology
Method used
Image
Examples
Embodiment Construction
[0016] First add 1 ton of waste phosphoric acid ≥ 25% (weight) in the neutralization kettle (1), then open the steam valve for heating, start the mixer and slowly add 280 kilograms of soda ash ≥ 98% (weight), when the temperature rises to ≥ When the temperature is 82°C and the pH value is 8±1, add ≥30% (weight) liquid caustic soda until the pH value is 12±1, the specific gravity is 1.2 and the temperature is >90°C, continue to stir for 5-20 minutes, and the liquid in the kettle will settle After 1 hour, send the settled liquid in the kettle to the neutralization kettle (2), [the upper suspension remains in the neutralization kettle (1), clean the neutralization kettle (1) every few times], and transfer to the neutralization kettle (1) Add 1 ton of ≥ 15% (weight) soda ash waste into the kettle (2), add 640 kilograms of phosphoric acid ≥ 85% (weight) at the same time, then add soda ash to adjust the neutralization degree K value (ratio of sodium / phosphorus) to 3.0 ±0.02 neutrali...
PUM
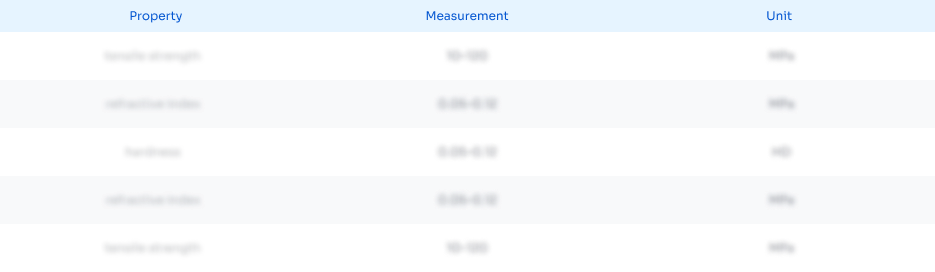
Abstract
Description
Claims
Application Information

- Generate Ideas
- Intellectual Property
- Life Sciences
- Materials
- Tech Scout
- Unparalleled Data Quality
- Higher Quality Content
- 60% Fewer Hallucinations
Browse by: Latest US Patents, China's latest patents, Technical Efficacy Thesaurus, Application Domain, Technology Topic, Popular Technical Reports.
© 2025 PatSnap. All rights reserved.Legal|Privacy policy|Modern Slavery Act Transparency Statement|Sitemap|About US| Contact US: help@patsnap.com