Technology for making oversleeve
A new process and sleeve technology, applied in clothing, clothing, protective clothing, etc., can solve the problems of high labor intensity, welding breakage, and low precision of workers, and achieve comfortable appearance and use effect, labor intensity improvement, and production efficiency. Effect
- Summary
- Abstract
- Description
- Claims
- Application Information
AI Technical Summary
Problems solved by technology
Method used
Image
Examples
Embodiment Construction
[0013] Now in conjunction with the accompanying drawings to illustrate, according to figure 1 A shows: in the direction of A→B→C motion trajectory, two layers of equal-width fabrics 2 and 2' are simultaneously released from the two unwinding axes, and eight elastic bands with the same tension are drawn out from eight elastic tubes at the same time 1 and 1', two as a group are attached to the four edges of the two-layer fabric at a constant velocity. figure 1 In B, apply hot melt adhesive to the elastic bands 1 and 1' at points A and A' (a and a'). If a braided elastic band is used, plastic welding can be implemented so that the elastic band is bonded to the non-woven fabric. at points B and B' (b and b'), butt-weld the second layer of fabric with elastic perpendicular to the plane to form weld 4; cut. The circular mechanical action of elastic fixing → fabric butt welding → welding seam cutting can automatically and continuously produce standard-sized disposable sleeves (see ...
PUM
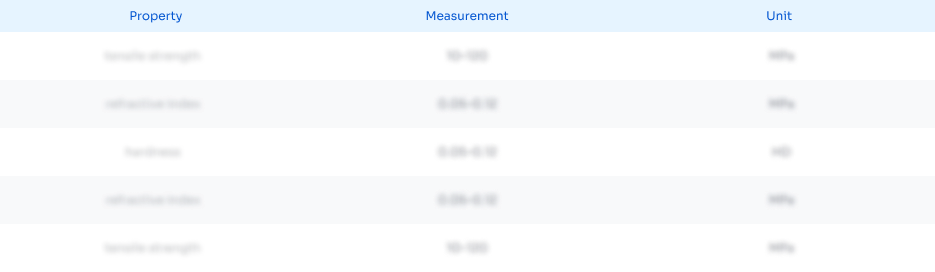
Abstract
Description
Claims
Application Information

- R&D
- Intellectual Property
- Life Sciences
- Materials
- Tech Scout
- Unparalleled Data Quality
- Higher Quality Content
- 60% Fewer Hallucinations
Browse by: Latest US Patents, China's latest patents, Technical Efficacy Thesaurus, Application Domain, Technology Topic, Popular Technical Reports.
© 2025 PatSnap. All rights reserved.Legal|Privacy policy|Modern Slavery Act Transparency Statement|Sitemap|About US| Contact US: help@patsnap.com