Modified cyanate ester resin and preparation method and uses thereof
A technology of cyanate resin and modified resin, which is applied in the field of modified cyanate resin and its preparation, can solve problems such as complex operation, and achieve good comprehensive performance, improved mechanical properties, and low water absorption.
- Summary
- Abstract
- Description
- Claims
- Application Information
AI Technical Summary
Problems solved by technology
Method used
Examples
preparation example Construction
[0030] The preparation method of modified resin cyanate ester of the present invention is that at first cyanate ester monomer is heated above melting point, makes it change into liquid state, then adds pre-mixed styrene and divinylbenzene under the situation of stirring, After stirring evenly, add an appropriate amount of stabilizer and allow it to cool naturally to obtain a homogeneous liquid modified resin. The resin has viscosity characteristics and working life that meet the requirements of RTM process operation at room temperature.
[0031] Catalysts and initiators can be dissolved in the modified resin without any solvent, and are generally added directly before the RTM process operation, and can be heated to promote their dissolution if necessary.
Embodiment 1
[0033] Styrene and divinylbenzene were premixed in a ratio of 100:30 parts by weight. Weigh 50 parts (weight) of bisphenol A cyanate in a beaker, heat and stir in an oil bath at 85°C to melt. Then add 33.3 parts of a mixture of styrene and divinylbenzene, stir evenly, cool naturally to 55°C, add 2% stabilizer, stir evenly, cool naturally to room temperature to obtain modified cyanate resin.
[0034] Add organotin catalyst and initiator to the above-mentioned modified cyanate resin, and heat the resin to 40°C to promote the dissolution of the catalyst and initiator, then pour it into a glass mold coated with a release agent in advance, and press the 90℃ / 3h+110℃ / 2h+130℃ / 2h+150℃ / 2h+180℃ / 2h+200℃ / 1h for curing. The properties of the modified cyanate resin and its cured products are listed in Table 1 and Table 2.
Embodiment 2
[0036] Same as Example 1, but with a 65:35 ratio of bisphenol A cyanate to a mixture of styrene and divinylbenzene. The properties of the modified cyanate ester resin and its cured product are shown in Table 1 and Table 2.
PUM
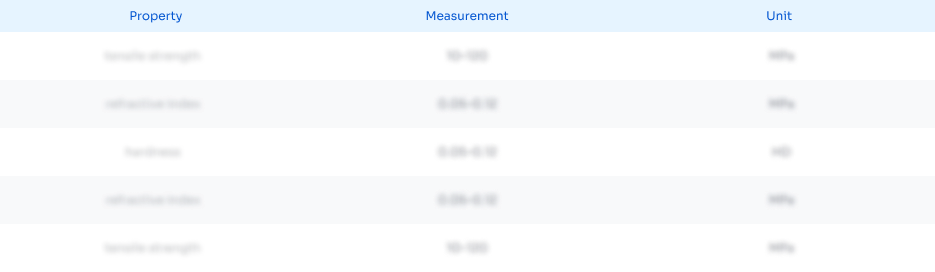
Abstract
Description
Claims
Application Information

- R&D
- Intellectual Property
- Life Sciences
- Materials
- Tech Scout
- Unparalleled Data Quality
- Higher Quality Content
- 60% Fewer Hallucinations
Browse by: Latest US Patents, China's latest patents, Technical Efficacy Thesaurus, Application Domain, Technology Topic, Popular Technical Reports.
© 2025 PatSnap. All rights reserved.Legal|Privacy policy|Modern Slavery Act Transparency Statement|Sitemap|About US| Contact US: help@patsnap.com