Wet & heat stretching method and apparatus for acrylonitrile fibre
An acrylonitrile-based, stretching device technology, applied in the direction of fiber chemical characteristics, textiles and papermaking, single-component synthetic polymer rayon, etc., can solve the problem of low stretching processing speed and coarsening of acrylic fiber bundles , Unable to perform uniform stretching and other problems
- Summary
- Abstract
- Description
- Claims
- Application Information
AI Technical Summary
Problems solved by technology
Method used
Image
Examples
Embodiment 1~28
[0055] (Examples 1-28, Comparative Examples 1-8)
[0056] An acrylonitrile-based copolymer with a reduced viscosity of 1.95 (acrylonitrile / vinyl acetate=93 / 7 weight ratio) was obtained by aqueous suspension polymerization. This was dissolved in dimethylacetamide so that the copolymer concentration was 25% by weight to prepare a spinning dope. This spinning dope was wet-spun in a spinning bath filled with a 40°C, 30% by weight aqueous solution of dimethylacetamide, and stretched once at a draw ratio of 5 times while washing the solvent in boiling water. . The drawn yarn having a swelling property of 80% after the first stretching was taken out and then dehydrated, and then neutralized (pH 8.3) in a 0.1% by weight sodium hydroxide aqueous solution.
[0057] Then, excess sodium hydroxide was washed to remove adhering oil agent, and then dried and densified with a hot roll at 150°C. Next, relaxation heat treatment was performed in pressurized steam of 250 kPaG to obtain an acry...
Embodiment 29~56 and comparative example 9~16
[0066] Except using the above-mentioned wet heat stretching device with the number of ejection ports changed as shown in Table 2, and supplying the acrylic fiber bundle after the relaxation heat treatment obtained by the same method as in Example 1 at a speed of 150 m / sec, the same method as in Example 1 was used. 1 Stretching was carried out under the same treatment conditions under different steam atmospheres with different steam injection states, to obtain acrylic fiber bundles having various steam shrinkage ratios in Examples 29 to 56 and Comparative Examples 9 to 16 shown in Table 2. Among them, the steam shrinkage rate of the obtained acrylic fiber bundle was measured 30 times, and the average shrinkage rate is shown in Table 2.
[0067] Acrylic fiber
total fineness of dimension
(kTex)
processing speed
(m / min)
For 1kg acrylonitrile
Steam volume of fiber bundle
(g)
Injection caliber
(mm)
Number of jets
Ejec...
PUM
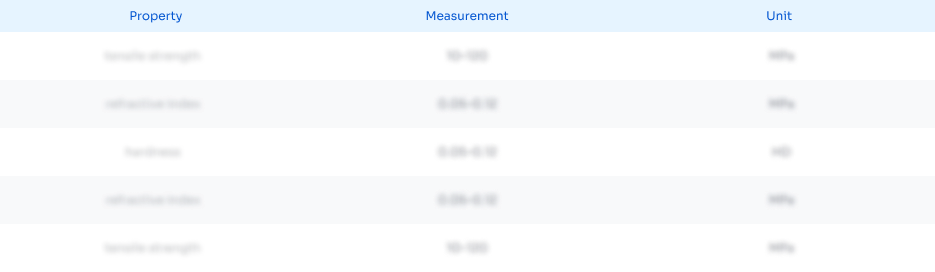
Abstract
Description
Claims
Application Information

- R&D
- Intellectual Property
- Life Sciences
- Materials
- Tech Scout
- Unparalleled Data Quality
- Higher Quality Content
- 60% Fewer Hallucinations
Browse by: Latest US Patents, China's latest patents, Technical Efficacy Thesaurus, Application Domain, Technology Topic, Popular Technical Reports.
© 2025 PatSnap. All rights reserved.Legal|Privacy policy|Modern Slavery Act Transparency Statement|Sitemap|About US| Contact US: help@patsnap.com